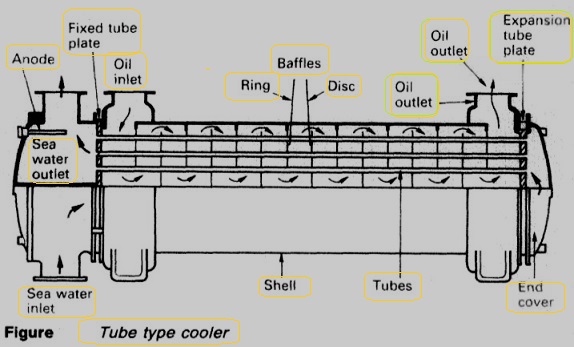
Fig 1 :Conventional tube type cooler
The usual method of securing the tubes in the tube plates is to roll-expand them. Tubes of aluminium brass (76% copper; 22% zinc; 2% aluminium) are commonly employed and the successful use of this material has apparently depended on the presence of a protective film of iron ions, formed along the tube length, by corrosion of iron in the system.
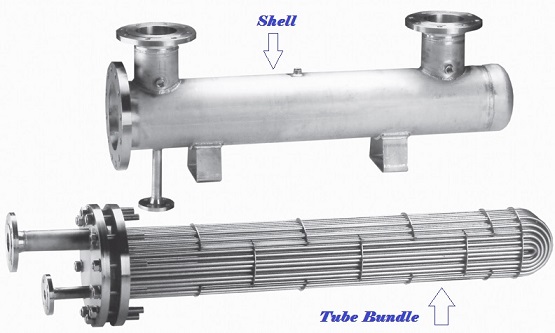
Fig: SHELL-AND-TUBE HEAT EXCHANGER