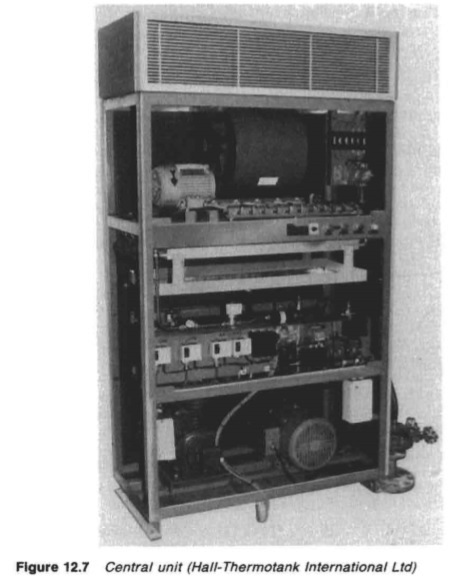
Figure : Marine air conditioning Central unit (Hall-Thermotank International Ltd)
Air distribution
Friction and eddy losses in the ducts make up the greater part of the pressure required at the fan, hence the design of the duct system affects the fan power very considerably. The fan power is a function of the air quantity and the pressure, and is expressed as follows:
The efficiency is static or total, depending on whether the pressure is static or total. The total pressure is the algebraic sum of the static and velocity pressures, The system is sized for the longest duct branch, so that artificial resistances must be inserted in other branches to balance the air distribution.
In designing the system, account is taken of static pressure regain to reduce the rate of fall along the ducts. This regain results from a reduction in velocity when the volume of air in the duct is reduced after an outlet is passed, and can amount to about 75% of the fall in velocity pressure.
High velocity distribution
Over the years, the most significant development has been the introduction of high velocity air distribution, made possible by the reduced air quantity
required. In other words, the inevitable increase in fan power associated with higher velocities (and hence higher pressures) has been kept within reasonable limits by a reduction in air quantity. High velocity distribution has a number of clear advantages among these being:
- Ducting costs much reduced.
- Standardizing on a few diameters of round ducting up to about 175 mm instead of a great variety of widths and depths of rectangular ducting,
- Standardized bends and fittings, having improved aerodynamic efficiencies.
- Use of automatic machines for fabrication of ducts, with a spiral joint giving great stiffness.
- Greatly reduced erection costs resulting from light weight and small bulk of ductwork.
- Considerable space saving in the ship.
- Possible reduced fire risk with smaller duct sections.
Against all these advantages must be set the increase in fan power already referred to. Thus an older system with duct velocities of the order of 8 m/s might require a fan pressure of no more than 50 mm water gauge, whereas with high velocities around 22.5 m/s the fan pressure could exceed 230 mm water gauge. The ratio of fan power increase is not so great as this, however, since high efficiency centrifugal fans of the backward-bent blade type are suited to high pressure operation, but for low pressures the relatively inefficient forward-bent blade type of fan must be used, since the high efficiency type fans would too bulky if designed for low pressures.
With the increase in friction loss due to high velocity, the reheating of the air can result in an appreciable increase in the cooling load, when compared with a low velocity system, and this could be a limiting factor in the choice of the duct velocity. The design of the air terminals is very important with high velocity distribution, in order to minimize noise and prevent draughts.
Duct insulation
Duct insulation is standard practice, being particularly necessary in installations where the policy has been to reduce the volume of air handled to a minimum, resulting in greater temperature differentials. The ideal is to integrate the insulation with the duct manufacture, or at least to apply it before the ductwork is despatched to the ship.
There are a number of high-class fire resistant insulating materials on the market, such as mineral wool and fibreglass. These, of course, must have a suitable covering to resist the entry of moisture and to protect the material from damage. Jointing of the duct sections is usually by sleeves, with external adhesive binding.
Summarized below some of the basic procedure of marine air conditioning system :
- Types of air conditioning system
Air conditioning systems may be divided into two main classes — the central unit type in which the air is distributed to a group of spaces through ducting, and the self-contained type, installed in the space it is to serve. .....
- Marine air conditioner
A very significant factor affecting an air conditioning system is the rapidly changing climatic conditions. The equipment has to perform within these variations and has to meet the differing requirements of the occupied spaces of the ship......
- Air conditioning central unit
The elements of a central unit are fan, filter, cooler, heaters and plenum chamber. Normally these are all housed within a single casing, with the possible exception of the fan. It is possible to carry this further by including the refrigerating plant in a single assembly thus providing a complete package. ....
- Air conditioning air terminals
The best designed air conditioning system is only as good as the means of delivering the air to the spaces. The main function of the air terminal is to distribute the air uniformly throughout the spaces without draughts......
- Heating and cooling loads and air quantities
Outside air must be introduced to all living spaces, although the amount of fresh air necessary to sustain life is very small indeed. Space conditions can vary greatly in a short time. They are governed by factors such as body odours and smoking, which may require a fresh air supply of 12 litre/s per person or more. ...
- Air conditioning unit typical specification
To prevent excessive leakage of conditioned air, all doors leading from the conditioned spaces to the outside atmosphere, machinery casing, etc., should be of the self-closing type and reasonably airtight......
Home page||
Cooling ||
Machinery||
Services ||
Valves ||
Pumps ||
Auxiliary Power ||
Propeller shaft ||
Steering gears ||
Ship stabilizers||
Refrigeration||
Air conditioning ||
Deck machinery||
Fire protection||
Ship design
||
Home ||
General Cargo Ship.com provide information on cargo ships various machinery systems -handling procedures, on board safety measures and some basic knowledge of cargo ships that might be useful for people working on board and those who working in the terminal. For any remarks please
Contact us
Copyright © 2010-2016 General Cargo Ship.com All rights reserved.
Terms and conditions of use
Read our privacy policy|| Home page||