Home page||Air conditioning ||
Typical specification for air conditioning installation in a general cargo ship or tanker
Installation serving the accommodation aft
The deck officers', engineer officers' and crew accommodation is served by two air conditioning units, with a direct expansion refrigerating plant of the Freon 22 type, capable of maintaining an inside condition of 26.7°C (d.b.) and 20.0°C (w.b.) (55% relative humidity) when the outside condition is 32.2°C (d.b.) and 28.9°C (w.b.) (78% relative humidity). Finned tube type steam heating coils are fitted to maintain 21°C in the space when the outside temperature is —-20,5°C. The schedule in Table 12.3 indicates the rates of air changes to be provided.
A proportion of the air would be recirculated except from the hospital, galley, pantries, laundry, shower rooms and toilets. The recirculated air is to be withdrawn through wire mesh grids mounted on mild steel ducting at deckhead level, located in the alley ways adjoining the treated space. With heating in operation, automatic temperature regulating valves in the steam supply lines give independent temperature control in the following spaces:
Officers: navigating bridge deck; bridge deck; boat deck; part poop deck.
Crew: part poop deck; upper deck.
The refrigerating plant comprises a compressor driven by a marine type motor with automatic starter, shell and tube type condenser, evaporator/air cooling
coils within the air conditioning unit casing, piping and fittings, safeguards, automatic cylinder unloading gear for cooling capacity control, and the initial charge of refrigerant. Mechanical and electrical spare gear is supplied.
Air conditioning units are installed on boat deck aft, with refrigerating machinery remotely situated in the engine room at middle flat level port side, approximately 7m above ship's keel, A sea-water circulating pump to serve the condenser is provided, The shipbuilder would supply and fit sea-water piping, and valves between the ship's side and pump, from pump to condenser and from condenser overboard, Air delivery to the spaces is by means of distributors, with sound attenuating chambers and air volume regulators, mounted on mild steel ducting at high level.
The cargo control room is served by a branch duct delivering 0.18 nvVsec through the distributors. Cooling at selected spots in the galley is provided by the conditioning units. Non-return valves are fitted in ducts serving hospital and laundries. This prevents odours reaching the accommodation should the fan unit be stopped for any reason.
Mechanical supply ventilation
Gyro and electronics room and motor generator room on bridge deck, switchboard room and telephone exchange on boat deck, motor room, storerooms and bedding store on upper deck, galley on poop deck are ventilated at atmospheric temperature by two axial flow supply fans. Air is delivered through diffusing type punkah louvres and domed diffusers fitted on mild steel ducts at deckhead level.
Mechanical exhaust ventilation
Galley, pantry, laundries, drying rooms, oilskin lockers, overall lockers, gyro and electronics room, motor gear room, switchboard room, telephone exchange and motor room and all private and communal toilets, washplaces, bathrooms and toilets, are ventilated by five axial flow exhaust fans. Hospital, medical locker, hospital toilet and bathroom must be independently ventilated by an axial flow exhaust fan. Vitiated air is withdrawn through domed extractors and regulating type grid openings mounted on mild steel ducting at deckhead level. Canopies over main galley range, should be supplied by the shipbuilder.
Air filtering equipment
Filter screens of washable nylon fibrous material are supplied with air conditioning and supply fan units. Spare screens would be provided.
General
All natural ventilation, together with shut-off valves as required, operating in conjunction with the mechanical system and serving spaces not mechanically ventilated, should be supplied and fitted by the shipbuilder. The shipbuilder provides the necessary air inlet and outlet jalousies to the unit compartment.
To prevent excessive leakage of conditioned air, all doors leading from the conditioned spaces to the outside atmosphere, machinery casing, etc., should be of the self-closing type and reasonably airtight. Cooling load calculations have been based on the understanding that there would be no awnings and that all accommodation would have airtight panelling on deckheads and house sides, and ship surfaces would be insulated by the shipbuilder as follows.
Approximate amount of insulation to be supplied and around ducting by shipbuilder: In accommodation 300 mz of 25 mm thick glass fibre slabs with vapour seal (or equivalent). Exposed deckheads 68.5 mm thick wood deck or equivalent thickness of insulation. Exposed sides 25 mm thick insulation suitably finished fitted on back of panelling or on steelwork around beams and stiffeners.
Galley surfaces Suitable insulation applied adjacent to conditioned spaces Surfaces of machinery spaces 50 mm thick insulation suitably finished. adjacent to conditioned spaces
All unit rooms in proximity to the accommodation should be suitably sound-insulated. The above proposal is exclusive of any ventilation whatsoever
to the forward pump, paint and lamp rooms and stores and also to the emergency generator room and battery room, book stores and CO2 bottle room.
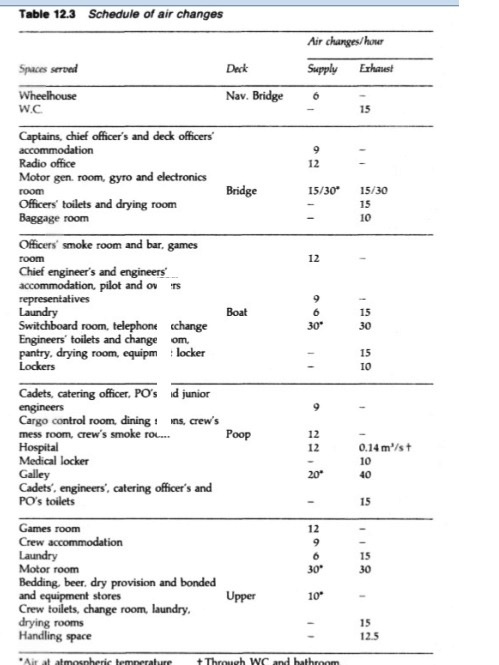
Figure : Air change schedule for general cargo ship accommodation
From Table 12.3 it will be observed that in certain of the air conditioned spaces, the air changes are less than those required by the Department of Transport First Schedule Regulation No. 1036, 1953, for ventilated spaces, Since the internal atmosphere achieved by conditioning the air would be superior to any under ventilation without artificial air cooling, it is understood from communication with the DTp that relaxation from the above requirements would be made by them under the terms of regulation 38(3) which provides for such relaxation in this event. The fitting of an installation as described above would, therefore, be subject to final approval of the Department of Transport.
Installation serving the engine control room
The engine control room would be served by three self-contained room
conditioners, to operate on 440 v, 3-phase, 60 Hz supply. Power consumption 1.2kW per unit. At least 7 litres/s of fresh air per occupant of room should be taken from machinery space system. The shipbuilder should pipe condenser cooling water from ship's services.
Erosion of condenser piping may be prevented by fitting a 'Constaflo' control valve in each unit to limit flow to 0.15 litre/s per unit. This proposal is exclusive of heating. The shipbuilder should supply and fit suitable bases for units, provide switches, wire up to motors and switches, and supply and fit cooling water drain piping and fittings.
Installation serving the cargo pump room
The cargo pump room is ventilated by two axial flow exhaust fans each to extract 1.4 mVs against 3.1 mbar static, requiring a total of 2.25 kW. The fans should be of split case bevel gear driven type enabling the fan motor to be mounted in the adjacent engine room. Motor and controller spare gear must be provided.
Air is extracted from two low level points through wire mesh grids fitted on galvanized steel ducting. The shipbuilder must supply and fit air outlet jalousies with hinged water tight covers, and natural ventilation to operate in conjunction with the mechanical system.
Further reading
Summarized below some of the basic procedure of marine air conditioning system :
- Types of air conditioning system
Air conditioning systems may be divided into two main classes — the central unit type in which the air is distributed to a group of spaces through ducting, and the self-contained type, installed in the space it is to serve. .....
- Marine air conditioner
A very significant factor affecting an air conditioning system is the rapidly changing climatic conditions. The equipment has to perform within these variations and has to meet the differing requirements of the occupied spaces of the ship......
- Air conditioning central unit
The elements of a central unit are fan, filter, cooler, heaters and plenum chamber. Normally these are all housed within a single casing, with the possible exception of the fan. It is possible to carry this further by including the refrigerating plant in a single assembly thus providing a complete package. ....
- Air conditioning air terminals
The best designed air conditioning system is only as good as the means of delivering the air to the spaces. The main function of the air terminal is to distribute the air uniformly throughout the spaces without draughts......
- Heating and cooling loads and air quantities
Outside air must be introduced to all living spaces, although the amount of fresh air necessary to sustain life is very small indeed. Space conditions can vary greatly in a short time. They are governed by factors such as body odours and smoking, which may require a fresh air supply of 12 litre/s per person or more. ...
- Air conditioning unit typical specification
To prevent excessive leakage of conditioned air, all doors leading from the conditioned spaces to the outside atmosphere, machinery casing, etc., should be of the self-closing type and reasonably airtight......
Home page||Cooling ||Machinery||Services ||Valves ||Pumps ||Auxiliary Power ||Propeller shaft ||Steering gears ||Ship stabilizers||Refrigeration||Air conditioning ||Deck machinery||Fire protection||Ship design
||Home ||
General Cargo Ship.com provide information on cargo ships various machinery systems -handling procedures, on board safety measures and some basic knowledge of cargo ships that might be useful for people working on board and those who working in the terminal. For any remarks please
Contact us
Copyright © 2010-2016 General Cargo Ship.com All rights reserved.
Terms and conditions of use
Read our privacy policy|| Home page||