Home page||Deck machinery||
Derricks and cargo winches -Ship cargo handling gears
Cargo handling:
The duty of a deck winch is to lift and lower a load by means of a fixed rope on
a barrel, or by means of whipping the load on the warp ends, to top or luff the
derricks, and to warp the ship. In fulfilling these duties it is essential that the
winch should be capable of carrying out the following requirements;
(a) lift the load at suitable speeds;
(b) hold the load from running back;
(c) lower the load under controlid)
take up the slack on the slings without undue stress;
(e) drop the load smartly on the skids by answering the operators application
without delay;
(f) allow the winch to be stalled when overloaded, and to start up again
automatically when the stress is reduced;
(g) have good acceleration and retardation.
In addition when the winch is electrically driven the requirements are:
(a) prevent the load being lowered at a speed which will damage the motor
armature;
(b) stop the load running back should the power supply fail;
(c) prevent the winch starting up again when the power is restored until the
controller has been turned to the correct position.
Hydraulic winch systems are quite common but electric drives for cargo
winches and cranes are most widely used. For the conventional Union Purchase
cargo handling arrangements or for slewing derrick systems handling loads up
to 20 tonne, standard cargo winches are normally used for hoist, topping and
slewing motions, the full load duties varying from 3—10 tonne at 0.65-0.3 m/s.
For the handling of heavy loads, although this may be accomplished with
conventional derrick systems using multi-part tackle, specially designed heavy
lift equipment is available. The winches used with these heavy lift systems may
have to be specially designed to fit in with the mast arrangements and the
winch duty pull may be as high as 30 tonne.
Cargo winches
It is usual to select the number and capacity of winches and to group them in
such a way that within practical limits, all hatches can be worked simultaneously
and having regard to their size (and the hold capacity beneath them) work at
each can be carried out in the same period.
Reduction of the cycle time during cargo handling is best accomplished by
the use of equipment offering high speeds say from 0.45 m/s at full load to
1.75 m/s light, the power required varying from 40 kW at 7 tonnes to 20 kW at
3 tonnes; this feature is available with electro-hydraulic and d.c. electric drives
as they offer an automatic load discrimination feature.
However, the
rationalization of electrical power supply on board ship has resulted in the
increased use of a.c. power and the majority of winch machinery now produced
for cargo handling utilizes the pole-change induction motor. This offers two or
more discrete speeds of operation in fixed gear and a mechanical change speed
gear is normally provided for half load conditions. Normally all modern cargo
handling machinery of the electric or electro-hydraulic type is designed to fail
safe. A typical application of this is the automatic application of the disc brake
on an electric driving motor should the supply fail or when the controller is
returned to the OFF position.
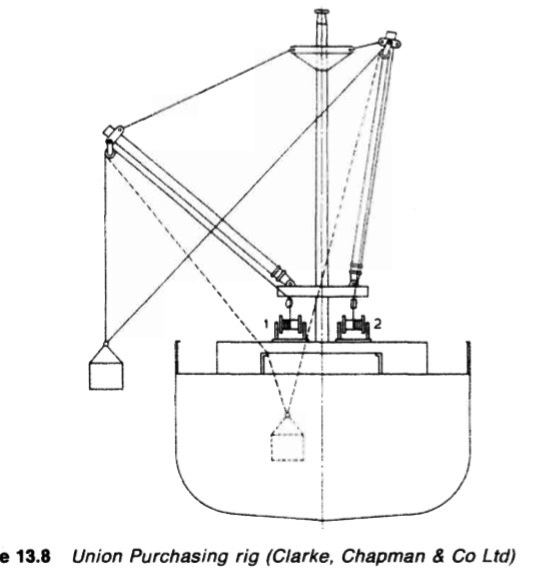
Figure 1: Union Purchasing rig (Clarke, Chapman & Co Ltd)
Derricks
Most older ships have winches in conjunction with derricks for working cargo.
The derricks may be arranged for fixed outreach working or slewing derricks
may be fitted. A fixed outreach system (Figure 1) uses two derricks, one
'topped' to a position over the ship's side and the other to a position over the
hold. The usual arrangement adopted, is known as the Union Purchase rig.
The
disadvantages of the fixed outreach system are that firstly if the outreach
requires adjustment cargo work must be interrupted, and secondly the load
that can be lifted is less than the safe working load of the derricks since an
indirect lift is used. Moreover considerable time and manpower is required to
prepare a ship for cargo working.
The main advantages of the system are that only two winches are required
for each pair of derricks and it has a faster cycle time than the slewing derrick
system.
The slewing derrick system, one type of which is shown in Figure 2 has
the advantages that there is no interruption in cargo work for adjustments and
that cargo can be more accurately placed in the hold. However in such a system
three winches are required for each derrick to hoist, luff and slew.
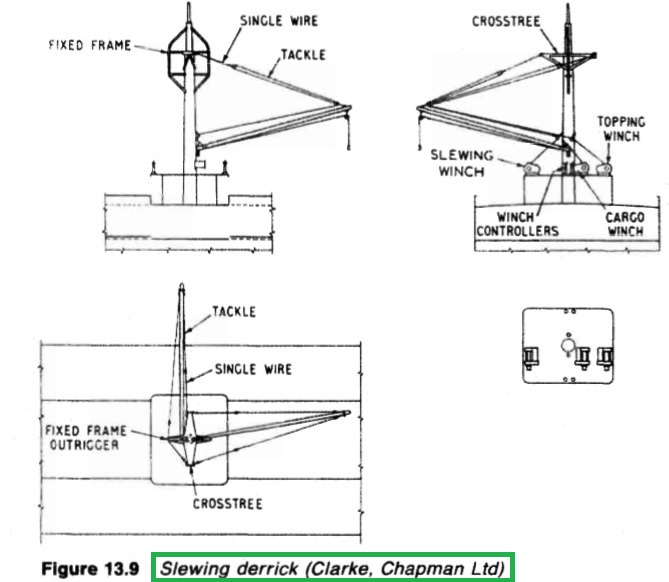
Figure 2 : Slewing derrick (Clarke, Chapman Ltd)
Summarized below some of the basic operation of deck machinery and maintenance guide :
- Powering deck machinery -Systems and components
Pump and motor systems are used for powering deck machinery such as
winches and windlasses. Pump and actuating cylinders are normally employed
for hatch covers. One or more pumps will be used to supply the volume of fluid
at the pressure required to operate one or more motors.
......
- Mooring equipment for general cargo vessel
The operation of mooring a vessel has traditionally required the attendance of
a large number of deck crew fore and aft. Supervision of the moorings was also
necessary to maintain correct tension through changes due to the tides and the
loading or unloading of cargo.
......
- Hydraulic systems for deck machinery and cargo equipment
The three essential components for a hydraulic circuit, are the hydraulic fluid
held in a reservoir tank, a pump to force the liquid through the system and a
motor or cylinder actuator to convert the energy of the moving liquid into a
working rotary or linear mechanical force. Valves to control liquid flow and
pressure are required by some systems.
......
- General cargo ship deck machinery electric drives
Electric motors on vulnerable deck areas may be protected against ingress of
water by being totally enclosed in a watertight casing. Vents are provided on
some winches, which must be opened when the motor is operating in port.
......
- Handling deck machinery- Anchor windlasses,Anchor capstan & mooring winches
The windlass cablelifter brakes must be able to control the running anchor
and cable when the cablelifter is disconnected from the gearing when
letting go'. Average cable speeds vary between 5 and 7 m/s during this
operation.
......
- General cargo ship deck deck crane
A large number of ships are fitted with deck cranes. These require less time to
prepare for working cargo than derricks and have the advantage of being able
to accurately place (or spot) cargo in the hold. On container ships using ports
without special container handling facilities, cranes with special container
handling gear are essential.
......
- Mechanically operated steel hatch covers
Hatch cover equipment like the other deck machinery, has to exist in a very
hostile environment and the importance of regular maintenance cannot be
over-emphasized. Drive boxes and electrical enclosures should be checked
regularly for water-tightness.
......
- Derricks and cargo winches -Ship cargo handling gears
The duty of a deck winch is to lift and lower a load by means of a fixed rope on
a barrel, or by means of whipping the load on the warp ends, to top or luff the
derricks, and to warp the ship.
......
Home page||Cooling ||Machinery||Services ||Valves ||Pumps ||Auxiliary Power ||Propeller shaft ||Steering gears ||Ship stabilizers||Refrigeration||Air conditioning ||Deck machinery||Fire protection||Ship design
||Home ||
General Cargo Ship.com provide information on cargo ships various machinery systems -handling procedures, on board safety measures and some basic knowledge of cargo ships that might be useful for people working on board and those who working in the terminal. For any remarks please
Contact us
Copyright © 2010-2016 General Cargo Ship.com All rights reserved.
Terms and conditions of use
Read our privacy policy|| Home page||