Home page||Ship employment
||
Modern cargo ships - Basic knowledge , ship type, design and facilities for cargo
Basic knowledge of general cargo ships
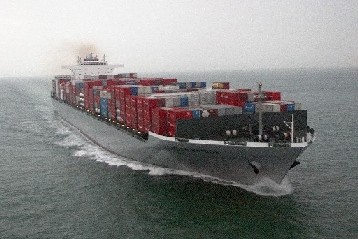
Modern dry cargo ship designs maximize hold space . A typical mid-size ship may have five or six holds; three or four
forward of the machinery space and superstructure, and one or two aft. The machinery spaces and superstructure are usually located about threequarters
aft. Older designs typically have three holds forward of the superstructure and two aft. Holds aft of the accommodation and machinery
spaces improve the trim of the vessel when partially loaded, and provide the ship with sufficient draft aft for stability and propeller immersion.
Small freighters often have machinery and accommodation spaces aft of all cargo holds. Deadweight of modern general cargo liners ranges
from 9,000 to 25,000 tons; speeds range from 17 to 22 knots. Tramps are typically smaller and slower, with speeds ranging from 12 to 18 knots.
The speed-to-length ratio is generally 0.87 or less as higher ratios are usually not economical. Laden drafts are as deep as channels to the
intended terminal ports allow, typically in the 26- to 29-foot range. Hull depth is selected to provide the desired draft and satisfy statutory
freeboard requirements. Depth of the double bottom is kept low to maximize cargo space.
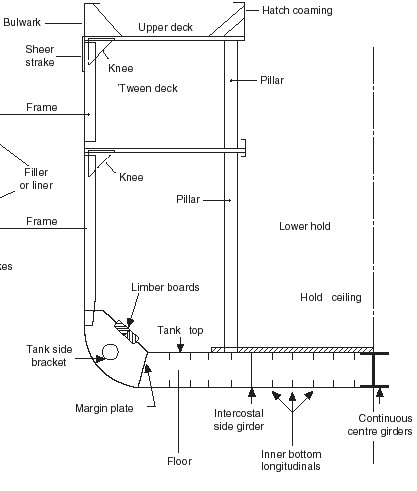
Fig:General cargo ships midship cross section
One or more ’tween decks may be fitted to facilitate flexibility in cargo loading
and unloading, cargo segregation, and to improve stability. There may be
watertight doors in the bulkheads on the ’tween decks levels. Denser cargoes are
carried in the lower holds with high stowage factor products normally stowed in
the ’tween decks. Refrigerated spaces may be built into the ’tween decks.
Tramps are designed to carry a wide variety of commodities while liners may be
designed for a specific trade. Ship designs for a specific trade strive for "full and
down" operation; the ship’s freeboard is down to her loadline with cargo cubic
fully occupied.
For a given trade, hold spaces are usually designed so that the
ratio of bale cubic to deadweight is 10 to 15 percent greater than the overall
stowage factor of the goods carried to allow for more rapid cargo handling and
broken stowage – the spaces between and around cargo units, including dunnage,
and spaces not available for cargo stowage because of physical obstructions or
ventilation and access requirements.
Holds are sized and provided with cargo
gear to limit the amount of cargo cubic per stevedore gang to about 60,000 cubic
feet; holds in the midbody are therefore usually shorter than those nearer the ends
of the ship. The conflict between the desire to shorten holds and the length
required by cargo gear and hatches sometimes dictates the assignment of midships
spaces to machinery or to fuel, cargo, or ballast deep tanks rather than holds.
Hatches are as large as possible without compromising hull strength (the main or
second deck is normally the strength deck) to reduce the requirement for
horizontal movement of cargo within the holds. Hatches served by two sets of
cargo gear generally measure 20 by 30 feet or larger. Hatches on older ships are
generally smaller than those on newer ships.
Hatches are surrounded by
coamings to reduce the risk of flooding in heavy seas. Covers are usually
constructed of steel (or wood on older vessels). The main deck plating between
hatches is not effective in providing longitudinal strength, and is sized to carry
fairly light local loads. The deck plating outboard the hatches is therefore much
heavier, often exceeding five-eighths inch in thickness.
Cargo gear is designed for speed and flexibility for handling breakbulk, palletized, or container cargo. Various combinations of derricks,
winches, and deck cranes are used for the handling of cargo. Cranes are fitted on many vessels to reduce manpower requirements. Some ships
have special heavy-lift derricks that may serve one or more holds. Booms are rigged for either yard and stay (burton) or swinging-boom
operation.
Various combinations of derricks, winches and deck cranes are used for the
Handling of cargo.
Basic Design of the Cargo Ship - Economic factors designing a new ship
The term “general (multipurpose) cargo ships” covers many
different ship designs that do not fit into other more specialised
cargo ship types. Thus, general cargo ships are not specialised
for transport of only dry bulks, only containers or only heavy-lift
cargoes, but they have flexibility to carry any of these cargo types.
General cargo ships are the world’s most numerous ship types,
excepting fishing vessels. Thus, in the year 2002 their share in the
overall world merchant fleet amounted to about 37% in numbers
and to about 11% in dwt.
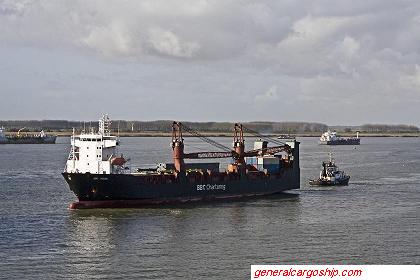
The average deadweight of the world fleet of general cargo
ships is about 5600 dwt. Larger vessels, up to about 30000 dwt are
intended to carry break-bulk cargo (bagged, boxed and palletised
cargo) or containers, while small general cargo ships, usually
below 5000 dwt are mostly found as flexible solutions for many
dry-cargo types in shortsea shipping.
The concern for structural safety of general cargo ships
follows from the fact that during the period from 1995 to 2000
approximately 90 losses of these ships per year occurred, which
in other words means one ship every 4 days, with 170 fatalities
per year. Even 42% of losses of all merchant ships belong to general
cargo ships and similar percentage is valid also for fatality
experience. Despite these figures, general cargo ships are not
considered in publicity as risky ships, probably because general
cargo ship accidents are not as spectacular as for example accidents
of oil tankers Erika or Prestige .
There are several reasons for poor statistical records of general
cargo ships. Ship ages, inappropriate maintenance, poor quality
in operation of these ships and defi ciencies in design are some of
the main causes of a large number of accidents. Smaller general
cargo ships are particularly vulnerable to collision and grounding
accidents because of their frequent operation in inland waterways
and coastal waters.
The general cargo ship consists of as large a clear open cargo-carrying space as possible,
together with the facilities required for loading and unloading the cargo.
Access to the cargo storage areas or holds is provided by openings in the deck called
hatches. Hatches are made as large as strength considerations will allow to reduce
horizontal movement of cargo within the ship.
Hatch covers of wood or steel, as in most modern ships, are used to close the hatch
openings when the ship is at sea. The hatch covers are made watertight and lie upon
coamings around the hatch which are set some distance from the upper or weather deck
to reduce the risk of flooding in heavy seas.
One or more separate decks are fitted in the cargo holds and are known as tween decks.
Greater flexibility in loading and unloading, together with cargo segregation and
improved stability, are possible using the tween deck spaces.
Various combinations of derricks, winches and deck cranes are used for the
Handling of cargo.
Designing a new cargo ship
The economic factor is of prime importance in designing a merchant
ship. An owner requires a ship which will give him the best possible
returns for his initial investment and running costs. This means that the
final design should be arrived at taking into account not only present
economic considerations, but also those likely to develop within the life
of the ship.
With the aid of computers it is possible to make a study of a large number
of varying design parameters and to arrive at a ship design which is not
only technically feasible but, more importantly, is the most economically
efficient.
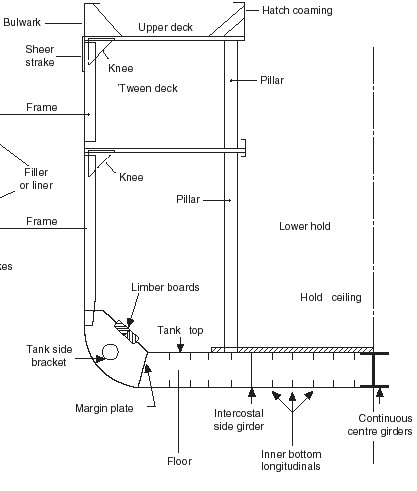
Fig:General cargo ships midship cross section
The initial design of a ship generally proceeds through three stages: concept;
preliminary; and contract design. The process of initial design is often
illustrated by the design spiral which indicates that given the
objectives of the design, the designer works towards the best solution
adjusting and balancing the interrelated parameters as he goes.
A concept design should, from the objectives, provide sufficient information
for a basic techno-economic assessment of the alternatives to be made.
Economic criteria that may be derived for commercial ship designs and
used to measure their profitability are net present value, discounted cash
flow or required freight rate. Preliminary design refines and analyses the
agreed concept design, fills out the arrangements and structure and aims
at optimizing service performance. At this stage the builder should have
sufficient information to tender. Contract design details the final arrangements
and systems agreed with the owner and satisfies the building
contract conditions.
Total design is not complete at this stage, it has only just started, postcontract
design entails in particular design for production where the
structure, outfit and systems are planned in detail to achieve a cost and
time effective building cycle. Production of the ship must also be given
consideration in the earlier design stages, particularly where it places
constraints on the design or can affect costs.
Ship Construction
The steel used in shipbuilding is mainly mild steel with 0.15-0.23% carbon content. Five grades of mild steel (A-E) are used ,manufactured, inspected, and tested under certain conditions. Finished steel is stamped by the classification societies.
High tensile steel is developed to have higher toughness,ductility, weldability, and strength.
This is developed by addition element such as vanadium, chromium, nickel, and Niobium.
Aluminum Alloys
Aluminum use in shipbuilding has increased due to the lighter weight (1/3 weight of steel). This
reduction of weight in the upper structure of the ship results in an improve of the ship stability.
Aluminum has a good resistance to corrosion. The main disadvantage of Aluminum is the high
cost.
Aluminum section are formed by extrusion. A special insulating arrangement is used when
joining steel to Aluminum.
Other useful articles :
- Assigning loadlines marks
Loadlines are marks punched into and painted on the sides of general cargo ships.The assigning of the vessels loadline and the issue of the Certificate is the
responsibility of the Marine Authority of the country. .
More .....
-
Cargo ships Loaded Condition
closely monitor the ship's condition during cargo
operations to ensure that if a significant deviation from the agreed loading/unloading
plan is detected all cargo and ballast operations must STOP..
More .....
-
Packing a container recommended method
Packing a container should always be done on level plane either on the ground,on a railcar, or on a trailer. In the case of a trailer, care should be taken to ensure the trailer cannot tip whilst being packed especially if a forklift truck is being used. If necessary the trailer should be propped. Brakes should be securely applied and wheels choked.
More .....
- Packing principles relating to cargo in containers
Where relevant, stowing should be carried out in a sequence which will permit
rapid checking and storage operations during and after unloading. Should the
consignment include cargo subject to customs pre-entry procedures, customs
examination would be made easier and unloading avoided if the cargo were
stowed at the end of the container by the door.
More .....
- Container Securing guidance
Containers have very little strength in any direction other than vertically
through the corner posts thus it is necessary to provide substantial support
to the containers when they are on the ship. Stowage of containers is with
their longer dimension fore and aft since the ship motion transmitted to
cargo is greater in rolling than pitching and it is therefore prudent to limit
any possible cargo movement within the container to the shorter transverse
dimension.
More .....
- Trim and stability booklet for cargo ships
Contain either curves of form or hydrostatic tables and stability and trim characteristics for various conditions of loading
.
More .....
- Broken stowage? Cargo ships guideline
The access shall be separate from the hatchway opening, and shall be by a stairway if possible. A fixed ladder, or a line of fixed rungs, shall have no point where they fill a reverse slope
.
More .....
-
Ship type, design and facilities for cargo
Cargo gear is designed for speed and flexibility for handling breakbulk, palletized, or container cargo. Various combinations of derricks,
winches, and deck cranes are used for the handling of cargo. Cranes are fitted on many vessels to reduce manpower requirements. Some ships
have special heavy-lift derricks that may serve one or more holds. Booms are rigged for either yard and stay (burton) or swinging-boom
operation.
More .....
- Cargo ships structural plans- how to use them
Structural plans, sometimes called scantlings plans, show dimensions of the ships framing and plating. The midships section drawing, generally available for all ships
More .....
Machinery system main info pages
Home page||Cooling ||Machinery||Services ||Valves ||Pumps ||Auxiliary Power ||Propeller shaft ||Steering gears ||Ship stabilizers||Refrigeration||Air conditioning ||Deck machinery||Fire protection||Ship employment
||
Home ||
General Cargo Ship.com provide information on cargo ships various machinery systems -handling procedures, on board safety measures and some basic knowledge of cargo ships that might be useful for people working on board and those who working in the terminal. For any remarks please
Contact us
Copyright © 2010-2016 General Cargo Ship.com All rights reserved.
Terms and conditions of use
Read our privacy policy|| Home page||