Home page||Ship employment
||
Use of derricks on board General cargo ships - safety procedure
Operation of derricks on board
Derricks for lifting cargo on board is required to be of adequate strength and stability for each load, having regard in particular to the stress induced at its mounting or fixing points , securely anchored, adequately ballasted or counterbalanced and supported by outriggers
as necessary to ensure its stability when lifting.
Ships' derricks should be properly rigged and employers and
masters should ensure that rigging plans are available containing the
following information:-
(1) position and size of deck eye-plates;
(2) position of inboard and outboard booms;
(3) maximum headroom (i.e. permissible height of cargo hook above hatch
coaming);
(4) maximum angle between runners;
(5) position, size and safe working load of blocks;
(6) length, size and safe working load of runners, topping lifts, guys and
preventers;
(7) safe working load of shackles;
(8) position of derricks producing maximum forces
(9) optimum position for guy and preventers to resist maximum forces as
at (h);
(10) combined load diagrams showing forces for a load of 1 tonne or the
safe working load;
(11) guidance on the maintenance of the derrick rig.
The operational guidance in the remainder of this section applies
generally to the conventional type of ship's derrick. For other types, such as
the "Hallen" and "Stulken" derricks, manufacturers' instructions should be
followed.
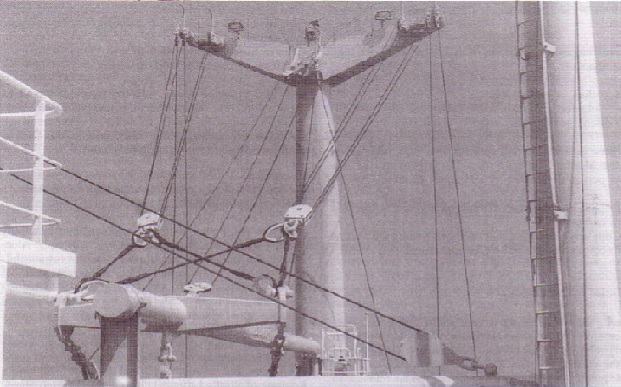
Figure 1:The rigging of Velle derrick with supporting mast
Runner guides should be fitted to all derricks so that when the
runner is slack, the bight is not a hazard to persons walking along the decks.
Where rollers are fitted to runner guides, they should rotate freely.
Before a derrick is raised or lowered, all persons on deck in the
vicinity should be warned so that no person stands in, or is in danger from,
bights of wire and other ropes. All necessary wires should be flaked out.
When a single span derrick is being raised, lowered or adjusted, the
hauling part of the topping lift or bull-wire (i.e. winch end whip) should be
adequately secured to the drum end.
The winch driver should raise or lower the derrick at a speed
consistent with the safe handling of the guys.
Before a derrick is raised, lowered or adjusted with a topping lift
purchase, the hauling part of the span should be flaked out for its entire
length in a safe manner. Someone should be available to assist the person
controlling the wire on the drum and keeping the wire clear of turns and in
making fast to the bitts or cleats. Where the hauling part of a topping lift
purchase is led to a derrick span winch, the bull-wire should be handled in
the same way.
To fasten the derrick in its final position, the topping lift purchase
should be secured to bitts or cleats by first putting on three complete turns
followed by four crossing turns and finally securing the whole with a lashing
to prevent the turns jumping off due to the wire's natural springiness.
When a derrick is lowered on a topping lift purchase, someone
should be detailed for lifting and holding the pawl bar, ready to release it
should the need arise; the pawl should be fully engaged before the topping
lift purchase or bull-wire is released. The person employed on this duty
should not attempt or be given any other task until this operation is
complete; in no circumstances should the pawl bar be wedged or lashed up.
A derrick with a topping winch, and particularly one that is self-
powered, should not be topped hard against the mast, table or clamp in such
a way that the initial heave required to free the pawl bar prior to lowering
the derrick cannot be achieved without putting an undue strain on the
topping lift purchase and its attachments.
A heel block should be secured additionally by means of a chain
or wire so that the block will be pulled into position under load but does
not drop when the load is released.
The derrick should be lowered to the deck or crutch and
properly secured whenever repairs or changes to the rig are to be carried
out.
If heavy cargo is to be dragged under deck with ship's winches,
the runner should be led directly from the heel block to avoid overloading
the derrick boom and rigging. Where a heavy load is to be removed, a snatch
block or bull wire should be used to provide a fair-lead for the runner and
to keep the load clear of obstructions.
Use of derricks in union purchase
When using union purchase the following precautions should be
strictly taken to avoid excessive tensions:-
(i) the angle between the married runners should not normally exceed
90° and an angle of 120° should never be exceeded;
(ii) the cargo sling should be kept as short as possible so as to clear the
bulwarks without the angle between the runners exceeding 90° (or
120° in special circumstances);
(iii) derricks should be topped as high as practicable consistent with safe
working;
(iv) the derricks should not be rigged further apart than is absolutely
necessary.
The following examples will show how rapidly loads increase on
derricks, runners and attachments as the angle between runners increases:
a) At 60° included angle, the tension in each runner would be just over
half the load;
b) At 90° the tension would be nearly three-quarters of the load;
c) At 195° the tension would be nearly 12 times the load.
When using union purchase, winch operators should wind in and
pay out in step, otherwise dangerous tensions may develop in the rig.
An adequate preventer guy should always be rigged on the
outboard side of each derrick when used in union purchase. The preventer
guy should be looped over the head of the derrick, and as close to and
parallel with the outboard guy as available fittings permit. Each guy should be
secured to individual and adequate deck or other fastenings.
Narrow angles between derricks and outboard guys and between
outboard guys and the vertical should be avoided in union purchase as
these materially increase the loading on the guys. The angle between the
outboard derrick and its outboard guy and preventer should not be too
large and may cause the outboard derrick to jack-knife. In general, the
inboard derrick guys and preventer should be secured as nearly as possible
at an angle of 90° to the derrick.
Use of stoppers
Where fitted, mechanical topping lift stoppers should be used.
Where chain stoppers are used, they should ALWAYS be applied by two
half-hitches in the form of a cow hitch suitably spaced with the remaining
chain and rope tail backed round the wire and held taut to the wire.
A chain stopper should be shackled as near as possible in line with
the span downhaul and always to an eyeplate, not passed round on a bight
which would induce bending stresses similar to those in a knotted chain.
No stopper should be shackled to the same eyeplate as the lead
block for the span downhaul; this is particularly hazardous when the lead
block has to be turned to take the downhaul to the winch or secure it to
bitts or cleats.
The span downhaul should always be eased to a stopper and the
stopper should take the weight before turns are removed from the winch,
bitts or cleats.
Overhaul of cargo gear
When a cargo block or shackle is replaced, care should be taken to
ensure that the replacement is of the correct type, size and safe working
load necessary for its intended use.
All shackles should have their pins effectively secured or seized
with wire.
A special check should be made on completion of the work to
ensure that all the split pins in blocks etc. have been replaced and secured.
On completion of the gear overhaul, all working places should be
cleaned of oil or grease.
Use of ships cargo gear
Typical cargo-handling gear is addressed under particular ship type headings, but some general arrangements can be noted here. General cargo ships are typically fitted with derricks or deck cranes to load or discharge cargo from piers or lighters without assistance. Most tankers discharge cargo with installed pumps and generally carry sufficient cargo hose to connect to receiving terminals; many
tankers have small derricks or cranes to handle the cargo hose.
Many ship types are gearless, that is, they are not fitted with cargo gear. Modern container ships rarely have the ability to handle their own
containers and can load and discharge cargo only with the aid of specialized port facilities. If installed, container ship cargo gear may consist
of conventional derricks or rotating cranes, or traveling overhead gantry cranes. Most bulk carriers are gearless although there are some selfunloaders
with installed derrick grabs or conveyor systems for discharging cargo, particularly on the Great Lakes. Roll-on/roll-off (RO/RO)
ships load cargo over ramps through stern, bow, or side ports; in the case of trailers, vehicles, and train cars, part of the cargo gear is integral
to the cargo itself.
When installed and operable, a vessel’s cargo gear can be a great asset to the salvage effort. Lightering is most effective and efficient when
accomplished with ship’s gear. The large number of derricks or cranes on general cargo ships facilitates loading salvage equipment and placing
it in its required location on deck or in holds. Deck mounted gantry cranes are particularly useful for shifting weight longitudinally to adjust
trim, weight distribution, or ground reaction; the cranes themselves are large weights that can be shifted.
More on general cargo ship :
- Rope handling safe procedure
Ropes are made of short fibres that are spun into yarns,
which are then made into flat or twisted strands.
And the strands are spun or braided to make the finished
rope .
More .....
-
Synthetic man-made ropes and hawsers
Although natural fibre ropes are still widely used throughout the marine industry, they have been superseded by synthetic fibres for a great many
purposes. Not only do the majority of synthetic ropes have greater strength
than their natural fibre counterparts, but they are more easily obtainable
and at present considerably cheaper.
More .....
-
Natural fibre rope
All natural fibre rope is manufactured from manilla, sisal, hemp, coir, cotton
or flax fibres.The process of manufacture consists of twisting the fibres
into yarns and turning the yarns in an opposite direction to establish the
strands.
More .....
-
Lay of Ropes and hawsers - Small Stuff descriptions
The lay of rope is a term used to describe the nature of the twist that produces the complete rope .The most common form of rope at sea is known as ‘hawser laid rope’ comprising three strands laid up right- or lefthanded.
More .....
- Stresses in ship structures and how to mitigate
Heavy weights tend to cause a downward deflection of the deck area supporting the load .This subsequently produces stresses, with
consequent inward and outward deflections of supporting bulkheads,
depending on the position of initial loading .
More .....
- Anchoring safe practice
Prior approaching an area for anchoring ships master should investigate fully a suitable anchoring position and conduct a planned approach including speed reduction in ample time and orienting the ships head prior anchoring to same as similar sized vessels around or stem the tide or wind whichever is stronger . Final decision to be made on method of anchoring to be used , the number of shackles , the depth of water, expected weather and holding ground. .
More .....
- MacGregor single-pull weather-deck hatch cover
Hatch covers are used to close off the hatch opening and make it
watertight. Wooden hatch covers, consisting of beams and boards over
the opening and covered with tarpaulins, were once used but are no
longer fitted. Steel hatch covers, comprising a number of linked steel
covers, are now fitted universally. Various designs exist for particular
applications, but most offer simple and quick opening and closing,
which speed up the cargo handling operation..
More .....
- Cargo holds access arrangement
The access shall be separate from the hatchway opening, and shall be by a stairway if possible. A fixed ladder, or a line of fixed rungs, shall have no point where they fill a reverse slope
.
More .....
- Prepare cargo holds prior loading
Washing is always carried out after the compartment has been swept. Drying time for washed compartments must be allowed for, before loading the next cargo; this time will vary with the climate, but two to three days must be expected.
More .....
- Strength and stability of the Lifting appliances
The vessel's structure, crane, derrick or other lifting device and the supporting structure should be of sufficient strength to withstand the loads
that will be imposed when operating at its maximum load moment .
More .....
- Lifting appliances - Maintenance, testing, controls & safety measures
When there is any suspicion that any appliance or item of
equipment may have been subjected to excessive loads, exceeding the Safe
Working Load (SWL), or subjected to treatment likely to cause damage, it
should be taken out of service until it can be subjected to a thorough
examination by a competent person.
More .....
- Safe operation of Lifting appliances and gears
All lifting operations must be properly planned, appropriately
supervised and carried out to protect the safety of workers.
More .....
- Derricks for lifting cargo on board
Derricks for lifting cargo on board is required to be of adequate strength and stability for each load, having regard in particular to the stress induced at its mounting or fixing points , securely anchored, adequately ballasted or counterbalanced and supported by outriggers
as necessary to ensure its stability when lifting.
More .....
- Deck cranes
Deck cranes have a number of advantages, the rigging
time being negligible, and the crane is able to pick up and land permitted
loads anywhere within its working radius. The safe working loads of cranes
is generally of the order of 10 to 15 tonnes and larger cranes are available
capable of lifts from 30 to 40 tonnes..
More .....
- Characteristics of Marine paints
Paint consists of pigment dispersed in a liquid referred to as the ‘vehicle’.
When spread out thinly the vehicle changes in time to an adherent dry film.
The drying may take place through one of the following processes..
More .....
- Protection by Means of Paints
It is often assumed that all paint coatings prevent attack on the metal
covered simply by excluding the corrosive agency, whether air or water. This
is often the main and sometimes the only form of protection; however there
are many paints which afford protection even though they present a porous
surface or contain various discontinuities. .
More .....
- Role classification societies maintaining seaworthiness of vessels
classification societies publish rules and regulations which are principally concerned with the strength of the ship, the provision of adequate equipment, and the reliability of the machinery .
More .....
- Periodic survey requirement by classification societies
To maintain the assigned class all steel ships are required to be surveyed and examined by the Society’s
surveyors at regular periods.
The major hull items to be examined at these surveys only are discussed
here..
More .....
Machinery system main info pages
Home page||Cooling ||Machinery||Services ||Valves ||Pumps ||Auxiliary Power ||Propeller shaft ||Steering gears ||Ship stabilizers||Refrigeration||Air conditioning ||Deck machinery||Fire protection||Ship employment
||
Home ||
General Cargo Ship.com provide information on cargo ships various machinery systems -handling procedures, on board safety measures and some basic knowledge of cargo ships that might be useful for people working on board and those who working in the terminal. For any remarks please
Contact us
Copyright © 2010-2016 General Cargo Ship.com All rights reserved.
Terms and conditions of use
Read our privacy policy|| Home page||