Home page||
How to prevent ships corrosion by Application of Marine paints
Protection by Means of Paints :
It is often assumed that all paint coatings prevent attack on the metal
covered simply by excluding the corrosive agency, whether air or water. This
is often the main and sometimes the only form of protection; however there
are many paints which afford protection even though they present a porous
surface or contain various discontinuities.
For example certain pigments in paints confer protection on steel even
where it is exposed at a discontinuity. If the reactions at the anode and cathode
of the corrosion cell which form positive and negative ions respectively,
are inhibited, protection is afforded. Good examples of pigments of this
type are red lead and zinc chromate, red lead being an anodic inhibitor,
and zinc chromate a cathodic inhibitor. A second mode of protection occurs
at gaps where the paint is richly pigmented with a metal anodic to the basis
metal. Zinc dust is a commercially available pigment which fulfils this
requirement for coating steel in a salt water environment. The zinc dust is
the sacrificial anode with respect to the steel.
Anti-fouling paints offer protection against vegetable and animal growth
which can lead to increased resistance requiring additional power, hence
fuel, to maintain the same speed. The greater the time spent at sea the less
the fouling; but areas of operation and seasons also decide the amount of
fouling, and with modern anti-fouling compounds the problem today is less
important.
Marine Paints
The paint system applied to any part of a
ship will be dictated by the environment to which that part of the structure
is exposed. Traditionally the painting of the external ship structure was
divided into three regions.
(i) Below the water-line where the plates are continually immersed in
sea water.
(ii) The water-line or boot topping region where immersion is intermittent
and a lot of abrasion occurs.
(iii) The topsides and superstructure exposed to an atmosphere laden
with salt spray, and subject to damage through cargo handling.
However now that tougher paints are used for the ship’s bottom the distinction
between regions need not be so well defined, one scheme covering
the bottom and water-line regions.
Internally by far the greatest problem is the provision of coatings for various
liquid cargo and salt water ballast tanks.
(a) Below the Water-line The ship’s bottom has priming coats of corrosioninhibiting
paint applied which are followed by an anti-fouling paint. Paints
used for steels immersed in sea water are required to resist alkaline conditions.
The reason for this is that an iron alloy immersed in a sodium chloride
solution having the necessary supply of dissolved oxygen gives rise to corrosion
cells with caustic soda produced at the cathodes.
Further the paint
should have a good electrical resistance so that the flow of corrosion currents
between the steel and sea water is limited. These requirements make the
standard non-marine structural steel primer red lead in linseed oil unsuitable
for ship use below the water-line. Suitable corrosion-inhibiting paints
for ships’ bottoms are pitch or bitumen types, chlorinated rubber, coal tar/
epoxy resin, or vinyl resin paints. The anti-fouling paints may be applied
after the corrosion-inhibiting coatings and should not come into direct
contact with the steel hull, since the toxic compounds present may cause
corrosion.
(b) Water-line or Boot Topping Region Generally modern practice requires
a complete paint system for the hull above the water-line. This may be
based on vinyl and alkyd resins or on polyurethane resin paints.
(c) Superstructures Red lead or zinc chromate based primers are commonly
used. White finishing paints are then used extensively for superstructures.
These are usually oleo-resinous or alkyd paints which may be based on ‘nonyellowing’
oils, linseed oil-based paints which yellow on exposure being
avoided on modern ships.
Where aluminium superstructures are fitted, under no circumstance
should lead based paints be applied; zinc chromate paints are generally
supplied for application to aluminium.
Temporary paint application during shipbuilding
After the
steel is blast cleaned it may be several months before it is built into the ship
and finally painted. It is desirable to protect the material against rusting in
this period as the final paint will offer the best protection when applied
over perfectly clean steel.
The formulation of a prefabrication primer for immediate application
after blasting must meet a number of requirements. It should dry rapidly to
permit handling of the plates within a few minutes, it should be non-toxic,
and it should not produce harmful porosity in welds nor give off obnoxious
fumes during welding or cutting. It must also be compatible with any subsequent
paint finishes to be applied. Satisfactory formulations are available,
for example a primer consisting of zinc dust in an epoxy resin.
Protection by Means of Paints
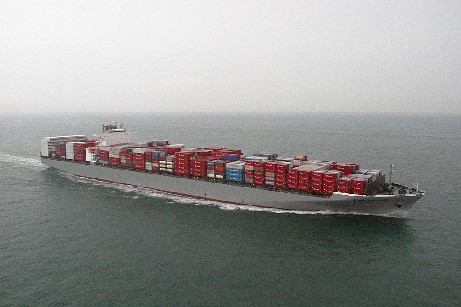
Good surface preparation is essential to
successful painting, the primary cause of many paint failures being the inadequacy
of the initial material preparation.
It is particularly important before painting new steel that any millscale
should be removed. Millscale is a thin layer of iron oxides which forms on
the steel surface during hot rolling of the plates and sections. Not only does
the non-uniform millscale set up corrosion cells as illustrated previously,
but it may also come away from the surface removing any paint film applied
over it.
The most common methods employed to prepare steel surfaces for painting
are:
i) Blast cleaning
ii) Pickling
iii) Flame cleaning
iv) Preparation by hand
Blast cleaning is the most efficient method for preparing the surface.
Following the blast cleaning it is desirable to brush the surface, and apply
a coat of priming paint as soon as possible since the metal is liable to rust
rapidly.
There are two main types of blasting equipment available, an impeller
wheel plant where the abrasive is thrown at high velocity against the metal
surface, and a nozzle type where a jet of abrasive impinges on the metal
surface. The latter type should preferably be fitted with vacuum recovery
equipment, rather than allow the spent abrasive and dust to be discharged
to atmosphere, as is often the case in ship repair work. Impeller wheel
plants which are self-contained and collect the dust and re-circulate the
clean abrasive are generally fitted within the shipbuilding shops.
Cast iron and steel grit, or steel shot which is preferred, may be used for
the abrasive, but non-metallic abrasives are also available. The use of sand
is prohibited in the United Kingdom because the fine dust produced may
cause silicosis.
Pickling involves the immersion of the metal in an acid solution,
usually hydrochloric or sulphuric acid in order to remove the millscale and
rust from the surface. After immersion in these acids the metal will require
a thorough hot water rinse. It is preferable that the treatment is followed by
application of a priming coat.
Using an oxy-acetylene flame the millscale and rust may be removed
from a steel surface. The process does not entirely remove the millscale and
rust, but it can be quite useful for cleaning plates under inclement weather
conditions, the flame drying out the plate.
Hand cleaning by various forms of wire brush is often not very satisfactory,
and would only be used where the millscale has been loosened by
weathering, i.e. exposure to atmosphere over a long period.
Blast cleaning is preferred for best results and economy in shipbuilding;
pickling which also gives good results can be expensive and less applicable
to production schemes; flame cleaning is much less effective; and hand
cleaning gives the worst results.
Paint hazards
Marine Paints may contain toxic or irritant substances, and the solvents may
give rise to flammable and potentially explosive vapours, which may also be
toxic. Personnel using such paints should be warned of the particular risks
arising from their use. Paints containing organic pesticides can be particularly
dangerous. If the manufacturer's instructions are not given on the container,
information should be obtained at the time of supply about any special
hazards, and also whether special methods of application should be followed.
Such advice should be readily available at the time of use but the following
precautions should always be taken.
Preparation and Precautions
Painted surfaces should always be rubbed down wet to reduce dust
from the old paint, which may be toxic if inhaled. Where the dust is known to
contain lead, other dust treating methods should be used. Dust masks should
be worn as protection against other dusts.
If the surface to be rubbed down is known to contain lead, then
methods that do not create dust should be adopted. It is safer to avoid or
minimise dust creation than to try to clean up the dust afterwards. Sanding or
abrasive blasting should be avoided. Lead based paint should never be burnt
off as fumes will contain metallic lead in a readily absorbed form.
Rust removers are acids and contact with unprotected skin should
be avoided. Eye protection should be worn against splashes .
If painting aloft or otherwise near ropes, care should be taken to avoid
splashes on ropes, safety harness, lines etc.
Interior and enclosed spaces should be well ventilated, both while
painting is in progress and until the paint has dried.
There should be no smoking or use of naked lights in interior
spaces during painting or until the paint has dried hard. Some vapours even in
low concentrations may decompose into more harmful substances when
passing through burning tobacco.
When painting is done in the vicinity of machinery or from an
overhead crane gantry, the power supply should be isolated and the machine
immobilised in such a way that it cannot be moved or started up
inadvertently. Appropriate warning notices should be posted .
Close-fitting clothing should be worn.
Use of Paint Spraying Equipment
As there are many different types of paint spraying equipment in
use, operatives should comply with the manufacturer's instructions for use.
Airless spray-painting equipment is particularly hazardous since the
paint is ejected at a very high pressure and can penetrate the skin or cause
serious eye injuries. Spray should not be allowed to come into contact with
the face or unprotected skin.
Suitable protective clothing such as a combination suit, gloves, cloth
hood, and eye protection should be worn during spraying.
Paints containing lead, mercury or similarly toxic compounds should
not be sprayed in interiors.
A suitable respirator should be worn according to the nature of the
paint being sprayed. In exceptional circumstances it may be necessary to use
breathing apparatus .
If a spray nozzle clogs, the trigger of the gun should be locked in a
closed position before any attempt is made to clear the blockage.
Before a blocked spray nozzle is removed or any other dismantling
is attempted, pressure should be relieved from the system.
When blowing through a reversible nozzle to remove a blockage, all
parts of the body should be kept clear of the nozzle mouth.
The pressure in the system should not exceed the recommended
working pressure of the hose. The system should be regularly inspected for
defects.
As an additional precaution against the hazards of a hose bursting, a
loose sleeve, for example a length of 2 to 3 meters (6 to 10 feet) of old air
hose, may be slipped over that portion of the line adjacent to the gun and
paint container.
To minimise risk of fire and to a lesser extent pollution, paint lockers are supposed to be kept clean. Areas of spilled paint must be cleaned immediately and shelves should be neatly stacked. Insofar as is possible, similar paint-types should be stored together with bars firmly in place, to prevent drums from jumping in bad weather.
More on general cargo ship :
- Rope handling safe procedure
Ropes are made of short fibres that are spun into yarns,
which are then made into flat or twisted strands.
And the strands are spun or braided to make the finished
rope .
More .....
-
Synthetic man-made ropes and hawsers
Although natural fibre ropes are still widely used throughout the marine industry, they have been superseded by synthetic fibres for a great many
purposes. Not only do the majority of synthetic ropes have greater strength
than their natural fibre counterparts, but they are more easily obtainable
and at present considerably cheaper.
More .....
-
Natural fibre rope
All natural fibre rope is manufactured from manilla, sisal, hemp, coir, cotton
or flax fibres.The process of manufacture consists of twisting the fibres
into yarns and turning the yarns in an opposite direction to establish the
strands.
More .....
-
Lay of Ropes and hawsers - Small Stuff descriptions
The lay of rope is a term used to describe the nature of the twist that produces the complete rope .The most common form of rope at sea is known as ‘hawser laid rope’ comprising three strands laid up right- or lefthanded.
More .....
- Stresses in ship structures and how to mitigate
Heavy weights tend to cause a downward deflection of the deck area supporting the load .This subsequently produces stresses, with
consequent inward and outward deflections of supporting bulkheads,
depending on the position of initial loading .
More .....
- Anchoring safe practice
Prior approaching an area for anchoring ships master should investigate fully a suitable anchoring position and conduct a planned approach including speed reduction in ample time and orienting the ships head prior anchoring to same as similar sized vessels around or stem the tide or wind whichever is stronger . Final decision to be made on method of anchoring to be used , the number of shackles , the depth of water, expected weather and holding ground. .
More .....
- MacGregor single-pull weather-deck hatch cover
Hatch covers are used to close off the hatch opening and make it
watertight. Wooden hatch covers, consisting of beams and boards over
the opening and covered with tarpaulins, were once used but are no
longer fitted. Steel hatch covers, comprising a number of linked steel
covers, are now fitted universally. Various designs exist for particular
applications, but most offer simple and quick opening and closing,
which speed up the cargo handling operation..
More .....
- Cargo holds access arrangement
The access shall be separate from the hatchway opening, and shall be by a stairway if possible. A fixed ladder, or a line of fixed rungs, shall have no point where they fill a reverse slope
.
More .....
- Prepare cargo holds prior loading
Washing is always carried out after the compartment has been swept. Drying time for washed compartments must be allowed for, before loading the next cargo; this time will vary with the climate, but two to three days must be expected.
More .....
- Strength and stability of the Lifting appliances
The vessel's structure, crane, derrick or other lifting device and the supporting structure should be of sufficient strength to withstand the loads
that will be imposed when operating at its maximum load moment .
More .....
- Lifting appliances - Maintenance, testing, controls & safety measures
When there is any suspicion that any appliance or item of
equipment may have been subjected to excessive loads, exceeding the Safe
Working Load (SWL), or subjected to treatment likely to cause damage, it
should be taken out of service until it can be subjected to a thorough
examination by a competent person.
More .....
- Safe operation of Lifting appliances and gears
All lifting operations must be properly planned, appropriately
supervised and carried out to protect the safety of workers.
More .....
- Derricks for lifting cargo on board
Derricks for lifting cargo on board is required to be of adequate strength and stability for each load, having regard in particular to the stress induced at its mounting or fixing points , securely anchored, adequately ballasted or counterbalanced and supported by outriggers
as necessary to ensure its stability when lifting.
More .....
- Deck cranes
Deck cranes have a number of advantages, the rigging
time being negligible, and the crane is able to pick up and land permitted
loads anywhere within its working radius. The safe working loads of cranes
is generally of the order of 10 to 15 tonnes and larger cranes are available
capable of lifts from 30 to 40 tonnes..
More .....
- Characteristics of Marine paints
Paint consists of pigment dispersed in a liquid referred to as the ‘vehicle’.
When spread out thinly the vehicle changes in time to an adherent dry film.
The drying may take place through one of the following processes..
More .....
- Protection by Means of Paints
It is often assumed that all paint coatings prevent attack on the metal
covered simply by excluding the corrosive agency, whether air or water. This
is often the main and sometimes the only form of protection; however there
are many paints which afford protection even though they present a porous
surface or contain various discontinuities. .
More .....
- Role classification societies maintaining seaworthiness of vessels
classification societies publish rules and regulations which are principally concerned with the strength of the ship, the provision of adequate equipment, and the reliability of the machinery .
More .....
- Periodic survey requirement by classification societies
To maintain the assigned class all steel ships are required to be surveyed and examined by the Society’s
surveyors at regular periods.
The major hull items to be examined at these surveys only are discussed
here..
More .....
Machinery system main info pages
Home page||Cooling ||Machinery||Services ||Valves ||Pumps ||Auxiliary Power ||Propeller shaft ||Steering gears ||Ship stabilizers||Refrigeration||Air conditioning ||Deck machinery||Fire protection||Ship employment
||
Home ||
General Cargo Ship.com provide information on cargo ships various machinery systems -handling procedures, on board safety measures and some basic knowledge of cargo ships that might be useful for people working on board and those who working in the terminal. For any remarks please
Contact us
Copyright © 2010-2016 General Cargo Ship.com All rights reserved.
Terms and conditions of use
Read our privacy policy|| Home page||