Home page||Ship employment
||
Heavy lift cargo handling - general cargo ship procedure
Heavy Indivisible Loads
Heavy indivisible loads may be defined as those which, because of their mass and/or shape cannot be
handled by the normal gear available on board ship or on the quay alongside. Containers of 20-30 tonnes
are handled rapidly and continuously at dedicated terminals where they are no longer considered heavy
lifts. However, in ports where specialist gear is not available, they may have to be treated and handled as
heavy lifts.
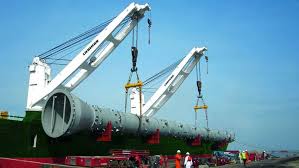
heavy lift cargo
The techniques for handling and transporting very heavy indivisible loads have changed and become
more specialised with the growth of the offshore industry, developments in onshore oil and chemical
plant construction and the move to gas-fired power stations. Although the offshore market has the largest
indivisible loads because they rarely move on land (other than a few metres to load out onto barges or semi-
submersibles) the other markets have taken to modular construction and technical advances have created
much heavier and denser loads. The newest gas turbine thermal blocks are over 550 tonnes in a small
concentrated area and oil refinery reactors are frequently over 1,400 tonnes in a single tower.
National road limits vary from country to country, but the controlling factors are usually bridges that have
to be crossed, elevated highway sections that cannot be shadowed by running underneath, or physical size
obstructing movement where just removal of street furniture is insufficient to clear a passage. In extreme
cases, buildings have been removed to allow passage and then rebuilt after movement.
Commercially, heavy lifts are divided into four groups for lift on/lift off operation. They are:- (a) under
200 tonnes,
- (b) 200499 tonnes,
- (c) 5001,600 tonnes, and
- (d) over 1,600 tonnes.
There is a large fleet
of vessels able to handle group (a) including many of the multi-purpose container feeder vessels and
some of the remaining traditional liner vessels. A reasonable number of these are able to handle group (b)
although many have restricted outreach. Group (c) is where the specialist heavy lift carriers take over as
the sole operators. There are presently (2011) heavy lift vessels in service with dual gear capable of lifting
2000 tonnes and new building orders are in place for two ships fitted with 2×1,100 tonnes cranes each and
thus able to lift up to 2,200 tonnes. Lifts in excess of 2,000 tonnes are usually handled by roll-on/roll-off
specialist vessels, including semi-submersibles being used as deck ships.
The Load
At the time of booking and pre-planning the transport of a heavy load, the following information is vital:
- a. the weight, size and construction (plans) of the load;
- b. the required (or permitted) support points for the load;
- c. the maximum permissible load for each support point;
- d. where and how the lifting attachments may be made on the load;
- e. the location of securing points on the load;
- f. any restrictions relating to the speed of movement of the load;
- g. details of additional lifting equipment required to handle the load including the provider, its
weight and whether it is to travel with the load;
- h. the position of the centre of gravity of the load which is crucial for major heavy lifts, particularly
when using multiple lifting gear;
- i. the heavy load itself should be prominently marked with its weight, centre of gravity and correct
slinging points on each side and on the top.
Shippers will normally require diagrams showing lifting stresses together with full lashing and securing
arrangements. In many cases this will be a charter party/booking note detail to be approved by both parties
before booking is concluded. Shippers will often require approval of the drawings by both their own
engineers and the warranty surveyor before lifting can proceed. Lashing and securing drawings will often
require accompanying calculations showing the anticipated maximum forces the cargo will experience
during transit on the vessel.
As wharves often have service ducting along the seaward margin, the authority at both loading and
discharge ports must specify the closest permitted point of approach to the edge on the wharf, which will
define the outreach needed from the ship. Some wharves will only permit landing of heavy cargo at high
tide and also require prompt removal while the tide is still high, to avoid excess stress on the structure.
Preparation
A mast or Sampson post supporting a traditional heavy lift derrick should, unless suitably stiffened,
be supported by not less than three stays; one leading in the fore and aft line and the others leading to
each side forming an angle of about 45° with the former. Stays and shrouds should be set up taut and
stretching screws securely stopped. A slack stay will not commence to function until after the mischief
has been done. Careful attention should be given to the ship's plans relating to the rigging and staying of
the heavy lift gear.
All leads should be set up to avoid chafing the falls. Avoid slack turns getting on to the winch barrel when
winding in slack wirethe presence of such is fraught with great danger when the derrick becomes loaded.
Where "steam guys" are led to a single winch, care must be taken to ensure that the weight of both remains
balanced, and that one does not become slack during any stage of the operation. It is sometimes the practice
to overcome this problem by securing the end of the topping lift purchase to a yoke which in turn supports
the end of each steam guy. Thus although the derrick may be topped or lowered a weight is maintained on
the steam guys no matter at what angle the derrick is operated. In these circumstances care must be taken
to ensure that the yoke is so positioned that it will operate correctly.
It is important that the vessel is trimmed to an upright position before heavy lift operations commence.
In many instances vessels are fitted with fast-flooding ballast transfer tanks. Additionally, the vessel should
not only be upright when lifting commences, but should, if possible, be maintained close to that position
throughout the operation by use of ballast tanks. When a vessel is working heavy cargo with its inherent risks,
all crew should be on deck and all non-essential shore personnel should be put ashore for their own safety.
The Gear
In the U.K. a heavy derrick, crane or hoisting machine with its gear, has to be tested with a proof load
which should exceed the safe working load as follows:
Safe Load Proof Load
Up to 20 tonnes 25% in excess
2050 tonnes 5 tonnes in excess
Over 50 tonnes 10% in excess
The gear should be adequate for the load, including any extra weight, e.g. for lifting tackle, which itself
may well weigh many tons.
The heavy lift derrick should not be operated in a depressed condition, i.e. near the horizontal, since if the
vertical component of the thrust becomes low, there is danger of the heel springing out of the shoe.
When using container cranes to handle uncontainerised heavy indivisible loads, there may be provision
for a "rams horn hook" to be installed in place of the container spreader. In some instances the spreader has
special lugs to which lifting wires may be shackled and the heavy lift supported directly by the spreader.
Where shore gantry cranes are used, it must be ascertained that the port of loading and port of discharge
have cranes of suitable capacity, with the necessary distance between the legs (and/or a revolving spreader)
to allow the load to be handled.
The gear in use should be exactly as indicated in the diagrams that have been approved by the shipper's
engineers or warranty surveyors and match the calculations that have been approved.
At all times check the validity of all parts of the lifting gear, including all loose items, before contracting
to lift.
Tackle
Slings should be made up of the appropriate wire or chain to provide an adequate safe working load, and
of the correct length so that they do not damage the cargo and do not require shortening because of too long
a drift.
The two ends of slings should be connected to the block of the derrick with the eyes on the bow of
the shackle and not on the pin, especially if the drift between lift and shackle is short and the spread
largewhich should be avoided where possible.
Slinging should be set up in such a way that the load remains level. However there may be occasions
when, to allow a particular awkwardly shaped load to enter the hatch square, the load will have to be
slung at an angle. If this is the case it must be ascertained that the load itself will not be damaged by such
treatment, and the slings made up accordingly.
Where goods may be become crushed, or where the length of the load is such that the angle of the sling
will create unacceptable bending moments on the load, the use of a spreader, or beam may be required.
As mentioned earlier the weight of any such tackle must be included in the calculations for the lifting gear.
Full use must be made of all proper lifting points on the load, and those points which are marked as
suitable for placing the sling.
Use only the certificated tackle as approved in the lifting and securing diagrams.
If, for any reason, an exact following of the lift and securing diagram is not possible and additional or
different tackle is required, err on the side of caution and use higher rated tackle. If new calculations can be
approved for lesser tackle then this can naturally be done, but always check all calculations done by others
before proceeding.
Vertical and Horizontal Movement
Careful winch driving is essential to avoid the gear being put to undue strain. Too great a speed of
operation increases the strain on the hauling part and may be dangerous if for any reason it should become
necessary to stop suddenly.
When lifting or lowering into or out of the hold, weight should be slowly taken up or lowered down so
as not to stress the gear.
When traversing either in or out of the hold from or to the shore the vessel should be maintained as close
as possible to upright using ballast.
When lifting from or lowering to the wharf, the weight must not be taken up or taken off by use of power
alone. If possible, when lowering a heavy load to the ground after just touching, when almost all of the
weight is still on the hook, the vessel should be ballasted further down to take the weight from the hook.
If this is not possible then a falling tide can do the same as ballasting down, but may be slightly slower.
Unwinding the weight too quickly direct from the winch will cause the vessel to heel and possibly drag the
heavy lift with it, creating dire consequences. When lifting, a rising tide can be used if de-ballasting is not
an option. In a closed dock situation, where moving ballast is not an option, then all movement should be
very slow and carefully monitored.
When transferring a heavy lift contracted for water/water movement, the calmest conditions possible
are needed and the added difficulties involved should be taken into account when contracting. Landing or
picking up a floating heavy lift in even a small swell puts excess stress on all parts if the equipment.
Stowage Requirements
The stowage position selected for a heavy lift must be that which can best support its weight. Additionally,
there may be a requirement to have the lift in such a position in the ship that the g-forces generated by
pitching and scending will not affect the load or its securing.
The load should be positioned so that heavy point loading is not exerted on deck or tank top plating
in between frames and beams. When this is not possible, bearers should be provided to spread the load.
Usually bearers are laid fore and aft or diagonally to achieve the maximum support from floors and beams.
Load spreading should take into account both the transverse frames and the longitudinal strengthening.
Heavy lifts should be stowed in a position that can be directly plumbed by the lifting hook so that
dragging is not required for either loading or discharge, i.e. in the hatch square of a general cargo ship.
Other factors to be considered to expedite the safe loading, carriage and discharge of a heavy lift are:
- The lift should be prominently marked with its weight, centre of gravity and lifting points
by the manufacturer prior to arriving alongside the ship. Items marked with conflicting
information, particularly regarding weight, should not be shipped until such information has been
verified;
- Individual heavy items should not be consolidated into a single unit using inadequate securing as
this will affect the requirements of 1 above and also risk an accident if securing fails;
- Individual lifts should not be tightly stowed leaving insufficient space for slinging at the discharge
port;
- The use of plenty of bearers and dunnage;
- Lifts must be handled and stowed in accordance with markings on each piece and/or instructions
from the shipper, e.g. "This way up" means exactly what it says.
In container ships (or general cargo ships so-fitted) pads provided for container stowage may be used
directly for the support of uncontainerised heavy lifts. Another method of supporting the lift is to use flat
rack platforms located in container stowage positions with the heavy lift placed on them. However, it
should be borne in mind that a heavy lift carried on the tank top of a cellular vessel will likely mean that the
container slots vertically above the lift are not available for loading.
Restraint
As mentioned earlier the cargo may have to be restrained during the loading operations particularly if it is
on a low friction device such as air or water skids. Once stowed in position lashing, securing and tomming
must be carried out to prevent the slightest movement of the load. All lashings must be set up tight and
wooden tomming must be secured in such a way that it cannot be dislodged by ship vibration, working or
movement. As a rule of thumb, a total lashing on one side of a load should have a combined breaking strain
of at least l½ times the total weight of the load to be restrained. Tomming and chocking would be extra to
this.
All lashing and tomming should utilise the appropriate and approved points on a load to give the support.
Where necessary extra securing points will have to be welded or riveted to ships' frames and decks.
Lashing and securing should follow the approved securing diagrams and gear used should be of the
specification detailed.
The higher the centre of gravity the more the heavy lift will tend to lift in a seaway, so sufficient downward
lashings are required.
Where possible, weld bracing to the deck to hold the load in position and any additional methods of
securing that can be welded direct to the deck/tank ceiling should be used. Always remember safety rules
when welding over tanks! Wooden tomming is insufficient on really heavy loads and steel restraints should
be used.
After completion of discharge remove all welded securing devices, grind smooth and coat to avoid damage.
Remember the underside of tank ceiling /deck plate will also have been damaged and need recoating.
Loading
The ship should be upright when loading (or discharging) a heavy lift and have adequate stability.
The double bottom tanks must be either pressed up or dry. If ship's gear is being used it must be remembered
that the effective centre of gravity of the load moves to the derrick head as soon as the lift is floated.
Lifting operations should be interrupted to carry out checks on the slinging arrangements:
a. as soon as the weight is taken by the slings.
b. when the load has been lifted a short distance.
The whole system should be checked through to ensure that no undue strain is being imposed on gear,
equipment, or the load itself.
Clear lines of communication should be established between all those involved in the operation, with one
person only in charge. It may be necessary to discontinue other operations close by on ship or shore to allow
those involved with the heavy lift to hear and understand the control signals.
Discharging
Similar precautions should be taken to those described under "Loading". Furthermore, it may be that the
vessel, being at the end of a voyage or passage, has less bottom weight in the form of fuel and/or water.
This will have to be taken into account when considering the stability requirements. It should also be borne
in mind that when a heavy lift is hoisted from its place of rest the centre of gravity of the weight is transferred
to the derrick head. Again it is important that one person only should be in charge of the operation and that
all activities are pre-planned with appropriate stops to check equipment and gear.
Occasionally heavy lift cargo has to be offloaded straight to the sea. This might be a requirement of semi-
submersible vessels or a requirement of the cargo itself e.g. lighters, launches, cylindrical and rectangular
tanks, etc. In such cases, provided that the pieces are of sufficiently strong and robust construction to
withstand the stresses and falls, they are carried on deck and launched over the side at destination.
Cylindrical objects, which must be perfectly watertight and free from small protruding parts, should
be mounted on a strong launching structure built of timber, the inboard end of which rests on top of the
adjacent hatch and the other on the bulwark, adequately supported at intermediate points. The frame of the
structure should incline about 2° in the direction of the ship's side.
The discharging is a simple process and is affected by listing the vessel in the desired direction by
means of water ballast or fuel oil. Tanks not in use for that purpose should either be empty or pressed up
and it should be borne in mind that when the weight drops off, the vessel will roll sharply in the opposite
direction.
For lighters, rectangular tanks, etc., a similar structure is built, extending a little beyond the bulwarks.
On top of the main structure a movable cradle-like arrangement is built to the shape of the craft so as to
support it at three or four different points, according to its length. This is mounted on launch or slipways
formed integral with the main structure with suitable means of locking it into position. The craft is secured
by wire lashings to prevent movement during transit and is launched overboard sideways by giving the ship
the necessary list.
After Discharge
It sometimes becomes necessary to unship stanchions when stowing heavy lift cargo. All such, forming
as they do important parts of the structural strength of the vessel, should be properly restored and secured
in their original position before stowing any cargo on the decks above.
When it is not possible or convenient to restore all stanchions into position without seriously embarrassing
the stowage, heavy shores of timber laid on stout timber fore and aft bearers should be fitted and tightly
wedged into position to carry the weight of the deck above. Neglect to do so will likely result in the deck
being set down.
Summarized below some more details on general cargo ship cargo handling procedure and operational info:
Cargo handling procedure for heavy indivisible loads
Heavy indivisible loads may be defined as those which, because of their mass and/or shape cannot be
handled by the normal gear available on board ship or on the quay alongside.
More .....
- Livestock handling brief procedure
The transport of animals is subject to legislation in many countries. Where risk of disease may exist this
legislation is rigorously enforced. In most cases the legislation not only covers the importation of animals,
but also the transit of animals, through a port.
More .....
- Unitised cargo handling technics for general cargo ship
A grouping together of two or more items (usually of a homogeneous nature) and securing them with
banding, glue, shrinkwrap, slings (e.g. clover leaf), to form a unit which, .
More .....
- Bagged Cargo handling procedure for general cargo ship
Bagged commodities need to be sufficiently robust to withstand external pressure and compression, as
the bag is designed to contain the contents rather than provide any substantial protection against external
damage. .
More .....
- Bales & bundles handling procedure for general cargo ship
Most baled commodities are impervious to damage from
rolling or dropping from limited heights. However, it can be dangerous to drop bales of rubber due to their
ability to bounce in any direction..
More .....
- Cases,Crates,Cartons, Drums,Barrels,Casks, etc.Handling technics
Cases and crates are usually constructed of plywood or thin low grade timber. Heavier cases may be built
up of 150mm×5mm (6×1) planks with strengthening pieces internally and externally while some are
built in a skeletal fashion to allow air to permeate through the contents and/or to reduce the weight. .
More .....
- DG Cargo handling procedure for general cargo ship
The IMDG Code recognises nine broad classes of Dangerous Goods. For the correct classification and
labelling of Dangerous Goods reference should be made to the IMDG Code. .
More .....
- Methods of ventilation used in general cargo ships
Ventilation of cargo may be necessary to remove heat, dissipate gas, help prevent condensation and/or
remove taint. Heat may be generated by live fruit, wet hides, vermin, and commodities liable to spontaneous
combustion .
More .....
- Methods of stowage used in general cargo ships
The stowage factor of any cargo is the volume which a certain amount in weight of
that cargo occupies. It is usually measures in cubic feet per long ton or alternatively in
cubic metres per metric ton. If the stowage factor is 20, it indicates a heavy cargo. If it
is 100, it indicates that the cargo is light.
More .....
- Special cargo handling in general cargo ships
Ventilation of cargo may be necessary to remove heat, dissipate gas, help prevent condensation and/or
remove taint. Heat may be generated by live fruit, wet hides, vermin, and commodities liable to spontaneous
combustion .
More .....
- Intermediate Bulk Containers ( I.B.C.)handling technics - general cargo ship procedure
An I.B.C. is a disposable or re-usable container designed for the carriage of bulk commodities in
parcels of between 0.5 and 3.0 tonnes.
More .....
- Dunnage requirement for general cargo ships
The traditional reasons for the use of dunnage have been largely superseded with the introduction of
containers and general cargo ships with shallower decks and holds.
More .....
- Methods of refrigeration used in general cargo ships
Refrigeration is essentially the removal of heat through
the process of evaporation. We choose to refrigerate
commodities such as fruits and vegetables because we
want to prolong their “practical shelf life” – the time from
harvest until the product loses its commercial value.
More .....
- Deck Cargo handling procedure for general cargo ship
A large variety of goods, because of their inherent properties (length, height, weight, etc.) may be carried
on deck. "On deck" means an uncovered space and includes deck houses having doors which can be
continuously open (except in heavy weather)..
More .....
Machinery system main info pages
Home page||Cooling ||Machinery||Services ||Valves ||Pumps ||Auxiliary Power ||Propeller shaft ||Steering gears ||Ship stabilizers||Refrigeration||Air conditioning ||Deck machinery||Fire protection||Ship employment
||
Home ||
General Cargo Ship.com provide information on cargo ships various machinery systems -handling procedures, on board safety measures and some basic knowledge of cargo ships that might be useful for people working on board and those who working in the terminal. For any remarks please
Contact us
Copyright © 2010-2016 General Cargo Ship.com All rights reserved.
Terms and conditions of use
Read our privacy policy|| Home page||