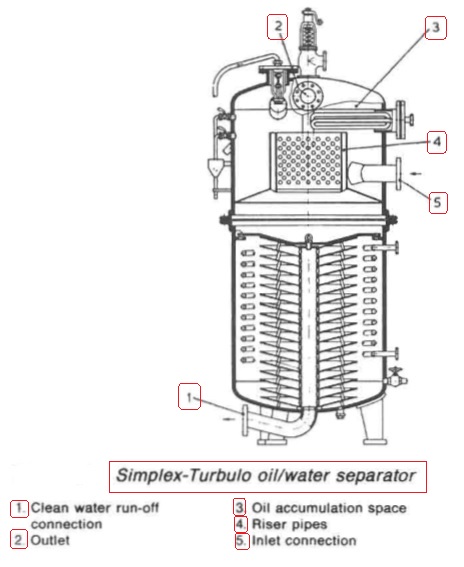
Figure 1: Simplex-Turbuto oil/water separator
The Simplex-Turbulo oil/water separator
The Simplex-Turbulo oil/water separator (Figure 1 ) consists of a vertical cylindrical pressure vessel containing a number of inverted conical plates. The oily water enters the separator in the upper half of the unit and is directed
downwards to the conical plates. Large globules of oil separate out in the upper part of the separator.
The smaller globules are carried by the water into the spaces between the plates. The rising velocity of the globules carries them upwards where they become trapped by the under-surfaces of the plates and coalesce until the enlarged globules have sufficient rising velocity to travel along the plate surface and break away at the periphery. The oil rises, is caught underneath an annular baffle and is then led up through the turbulent inlet area by risers to collect in the dome of the separator.
The water leaves the conical plate pack via a central pipe which is connected to a flange at the base of the separator, Two test cocks are provided to observe the depth of oil collected in the separator dome. When oil is seen at the lower test cock, the oil drain valve must be opened. An automatic air release valve is located in the separator dome. An electronically operated oil drainage valve is also frequently fitted. This works on an electric signal given be liquid level probes in the separator. Visual and audible oil overload indicators may also be fitted. To assist separation steam coils or electric heaters are fitted in the upper part of the separator. Where high viscosity oils are to be separated additional heating coils are installed in the lower part.
Before initial operation, the separator must be filled with clean water. To a large extent the conical plates are self-cleaning but periodically the top of the vessel should be removed and the plates examined for sludge build-up and corrosion. It is important that neither this separator nor any other type is run at over capacity.
When a separator is overloaded the flow becomes turbulent, causing re-entrainment of the oil and consequent deterioration of the effluent quality. To meet the requirement of legislation which came into force in October 1983 and which requires that the oil content of bilge discharges be reduced in general to 100 ppm and to 15 ppm in special areas and within 12 nautical miles of land, a second stage coalescer (Figure below) was added in some designs. Filter elements in the second stage remove any small droplets of oil in the discharge and cause them to be held until they form larger droplets (coalesce). As the larger globules form, they rise to the oil collecting space.
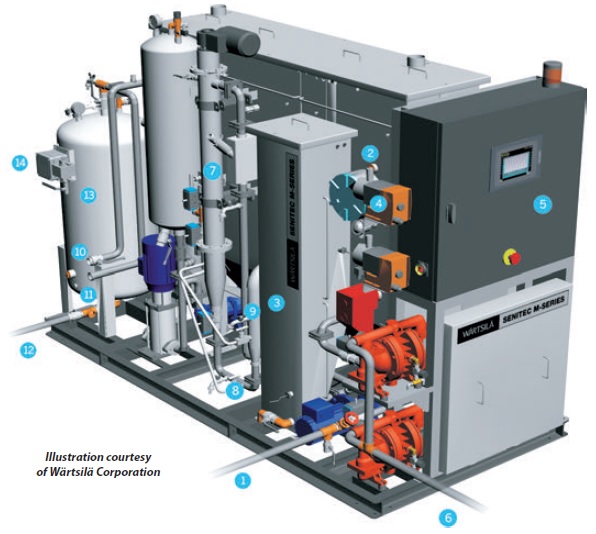
Fig: Oily water separator WÄRTSILÄ SENITEC M1000, capacity 1 m3/hour