Home page||General service system ||
Reason for distillate treatment-Chlorine sterilization and conditioning
Reason for distillate treatment :The low operating temperature of the evaporator , is not sufficient to sterilize the product. Despite precautions near the coast, harmful organisms may enter with the sea water and pass through to the domestic water tank and system. Additionally there is a likelihood that while in the domestic tank, water may become infested with bacteria, due to a build up of a colony of organisms from some initial contamination.
Sterilization by the addition of chlorine, is recommended in Merchant Shipping Notice M1214. A later notice, M1401, states that the Electro-Katadyn process in use since the 1960s, has also been approved. Another problem with distilled water is that having none of the dissolved solids common in fresh water it tastes flat. It also tends to be slightly acidic due to its ready absorption of carbon dioxide (CO2). This condition makes it corrosive to pipe systems and less than beneficial to the human digestive tract.
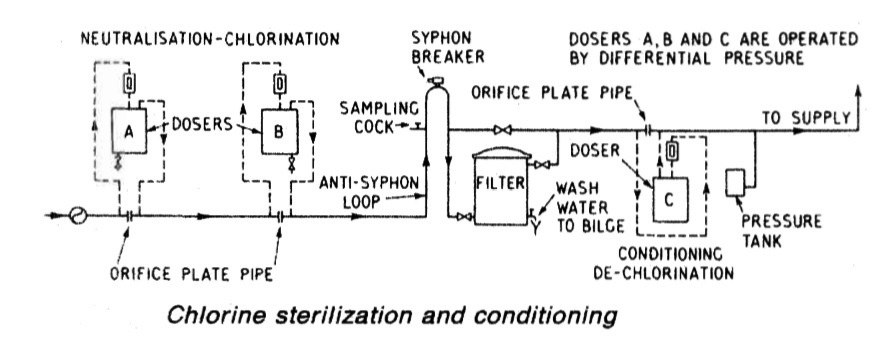
Figure 1: Chlorine sterilization and conditioning
Chlorine sterilization and conditioning
Initial treatment (Figure 1) involves passing the distillate through a neutralite unit containing magnesium and calcium carbonate. Some absorption of carbon dioxide from the water and the neutralizing effect of these compounds, removes acidity. The addition of hardness salts also gives the water a better taste.
The sterilizing agent chlorine, being a gas, is carried into the water as a constituent of sodium hypochlorite (a liquid) or in granules of calcium chloride dissolved in water. The addition is set to bring chlorine content to 0.2 ppm. While the water resides in the domestic tank, chlorine should preserve sterility. In the long term, it will evaporate so that further additions of chlorine may be needed. The passage of water from storage tanks to the domestic system, is by way of a carbon filter which removes the chlorine taste.
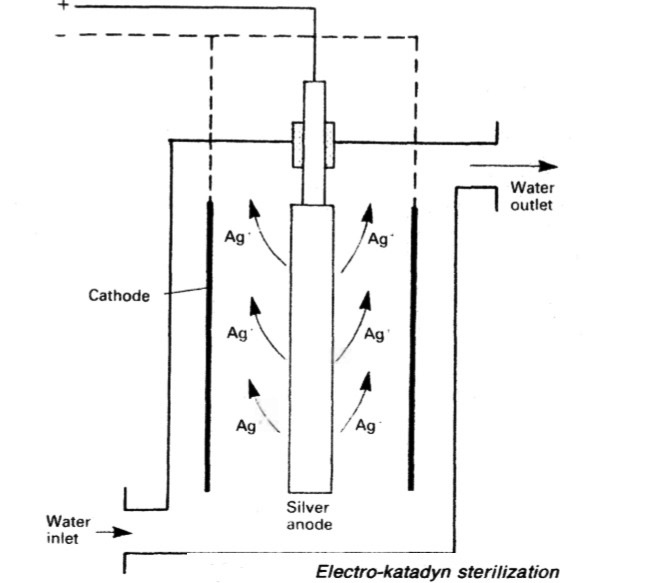
Figure 2: Electro-katadyn sterilization
Electro-katadyn method of sterilization
The Electro-katadyn process (Figure 2) accepted as an alternative to chlorination (see M1401) involves the use of a driven silver anode to inject silver ions (Ag+) into the distilled water product of the low temperature evaporator.
Silver is toxic to the various risk organisms. Unlike the gas chlorine, it will not evaporate but remains suspended in the water. The sterilizer is placed close to the production equipment with the conditioning unit being installed after the sterilizer and before the storage tank. The amount of metal released to water passing through the unit, is controlled by the current setting. If a large volume has to be treated, only part is bypassed through and a high current setting is used to inject a large amount of silver.
The bypassed water is then added to the rest in the pipeline. With tow water flow, all of the water is delivered through the device and the current setting is such as to give a concentration of 0.1 ppm of silver. The silver content of water in the domestic system, should be 0.08 ppm maximum.
Ultra-violet sterilizer
A means for sterilizing potable water at the point of use, is provided on many offshore installations and ships, by an ultra-violet radiation unit which is positioned after the hydrophore tank and as close as possible to the tap supply points.
The stainless steel irradiation chamber contains low pressure mercury vapour tubes, housed in a quartz jacket. Tubes are wired in series with a transformer for safety. A wiper is fitted within the chamber to clean the jackets and lamp observation window. Units of a similar type are used for pretreatment disinfection in some reverse osmosis plant.
Summarized below some of the basic procedure of machinery service systems and equipment :
- Ballast arrangements
The ballasting of a vessel which is to proceed without cargo to the loading port is necessary for a safe voyage, sometimes in heavy weather conditions. On arrival at the port the large amount of ballast must be discharged rapidly in readiness for loading....
- Cargo ships bilge systems
The essential purpose of a bilge system, is to clear water from the ship's 'dry' compartments, in emergency. The major uses of the system, are for clearing water and oil which accumulates in machinery space bilges as the result of leakage or draining, and when washing down dry cargo holds. The bilge main in the engine room, has connections from dry cargo holds, tunnel and machinery spaces.....
- Bilge system layout details
All bilge suctions have screw down non-return valves with strainers or mud boxes at the bilge wells. Oily bilges and purifier sludge tanks have suitable connections for discharge to the oily water separator or ashore. The system is tailored to suit the particular ship......
- Domestic water system
Systems using gravity tanks to provide a head for domestic fresh and sanitary water, have long been superseded by schemes where supply pressure is maintained by a cushion of compressed air in the service tanks....
- Reverse osmosis
Osmosis is the term used to describe the natural migration of water from one side of a semi-permeable membrane into a solution on the other side. The
phenomenon occurs when moisture from the soil passes through the membrane covering of the roots of plants,....
- Salinometer features
The condensate or product, if of acceptable quality, is delivered to the appropriate tanks by the distilled water pump. Quality is continuously tested by the salinometer both at start up and during operation. If the device registers an excess of salinity it will dump the product and activate the alarm using its solenoid valves. The product is recirculated in some installations......
- Sewage systems
The exact amount of sewage and waste water flow generated on board ship is difficult to quantify. European designers tend to work on the basis of 70 litres/person/day of toilet waste (including flushing water) and about 130-150 litres/person/day of washing water (including baths, laundries, etc.). US authorities suggest that the flow from toilet discharges is as high as 114 litres/person/day with twice this amount of washing water......
- Sewage zero discharge system
A retention or holding tank is required where no discharge of treated or untreated sewage is allowed in a port area. The sewage is pumped out to shore reception facilities or overboard when the vessel is proceeding on passage at sea, usually beyond the 12 nautical mile limit. ...
- Biological sewage treatment
A number of biological sewage treatment plant types are in use at sea but nearly all work on what is called the extended aeration process. Basically this consists of oxygenating by bubbling air through or by agitating the surface. ....
- Sterilization system
Sterilization by the addition of chlorine, is recommended in Merchant Shipping Notice M1214. A later notice, M1401, states that the Electro-Katadyn process in use since the 1960s, has also been approved. Another problem with distilled water is that having none of the dissolved solids common in fresh water it tastes flat. It also tends to be slightly acidic due to its ready absorption of carbon dioxide (CO2). .....
- Treatment of water from shore
There is a risk that water supplied from ashore may contain harmful organisms which can multiply and infect drinking or washing water storage tanks. All water from ashore, whether for drinking or washing purposes, is to be sterilized. When chlorine is used, the dose must be such as to give a concentration of 0.2 ppm....
- Water production low pressure evaporator
A considerable amount of fresh water is consumed in a ship. The crew uses on average about 70 litre/person/day and in a passenger ship, consumption can be as high as 225 litre/person/day. Water used in the machinery spaces as make up for cooling system losses may be fresh or distilled but distilled water is essential for steam plant where there is a water tube boiler.
Steamship consumption for the propulsion plant and hotel services can be as high as 50 tonnes/day.....
- Flash evaporator system
The evaporator , boils sea water at the saturation temperature corresponding to the uniform pressure through the evaporation and condensing chambers. With flash evaporators the water is heated in one compartment before being released into a second chamber in which the pressure is substantially lower......
- Oil content monitor system
In the past, an inspection glass, fitted in the overboard discharge pipe of the oil/water separator permitted sighting of the flow. The discharge was illuminated by a light bulb fitted on the outside of the glass port opposite the viewer......
- Oily water separator
Oil/water separators are necessary aboard vessels to prevent the discharge of oil overboard mainly when pumping out bilges. They also find service when deballasting or when cleaning oil tanks. The requirement to fit such devices is the result of international legislation....
Home page||Cooling ||Machinery||Services ||Valves ||Pumps ||Auxiliary Power ||Propeller shaft ||Steering gears ||Ship stabilizers||Refrigeration||Air conditioning ||Deck machinery||Fire protection||Ship design
||Home ||
General Cargo Ship.com provide information on cargo ships various machinery systems -handling procedures, on board safety measures and some basic knowledge of cargo ships that might be useful for people working on board and those who working in the terminal. For any remarks please
Contact us
Copyright © 2010-2016 General Cargo Ship.com All rights reserved.
Terms and conditions of use
Read our privacy policy|| Home page||