Home page||Refrigeration system||
Refrigeration systems expansion valves
Expansion valves
The expansion valve is the regulator through which the refrigerant passes from the high pressure side of the system to the low pressure side. The pressure drop causes the evaporating temperature of the refrigerant to fall below that of the evaporator. Thus, for example, the refrigerant can be boiled off by an evaporator temperature of — 18 deg C because the pressure drop brings the evaporating temperature of the refrigerant down to say — 24 deg C The liquid refrigerant leaves the condenser with a temperature just above that of the sea-water inlet, say 15 deg C. As it passes through the expansion valve the evaporating temperature decreases to — 24 deg C and some of the liquid boils off taking its latent heat from the remainder of the liquid and reducing its temperature to below that of the evaporator. There are six basic types of refrigerant controls or expansion devices, which can be summarized as follows.
Manually operated expansion valves
These were used for CO2 refrigeration installations where the compressor was started and stopped by a watchkeeper. The compressor was started with the expansion valve open. The valve was then closed in to bring up pressure on the condenser side until the saturation or condensing temperature for the pressure (shown on the gauge) was five or six degrees above that of the cooling sea water.
After the manual expansion valve had been set in this way, the gauge on the compressor suction (or evaporator side) was checked. Equivalent saturation or boiling temperature shown for the suction or evaporator pressure had to be about five or six degrees lower than the brine temperature. Any discrepancy indicated undercharge due to CO2 leakage or overcharge due to over enthusiastic topping up with gas. Many modern refrigeration systems have an emergency expansion valve which can be set manually in a similar way.
Manually operated expansion valves have the disadvantage of being unresponsive to changes in load or sea-water temperature and must be adjusted frequently. The valve itself is a screw down needle valve dimensioned to give fine adjustment.
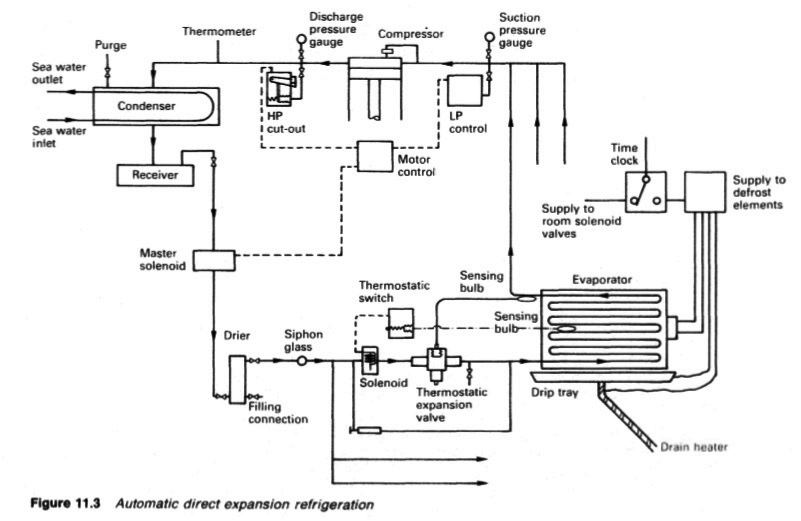
Figure 11.3 : Automatic direct expansion refrigeration
Automatic expansion valves
These consist of a needle with seat and a pressure bellows or diaphragm with a torsion spring capable of adjustment. Operated by evaporator pressure their chief disadvantage is their relatively poor efficiency compared with other types.
Constant pressure in the evaporator also requires a constant rate of
vaporization, which in turn calls for severe throttling of the liquid. There is also the danger of liquid being allowed to return to the compressor when the load falls below a certain level This type of valve is used principally in small equipment with fairly constant loads, such as domestic storage cabinets and freezers.
Thermostattc expansion valves
These valves are similar in general design to automatic valves, but having the space above the bellows or diaphragm filled with the liquid refrigerant used in the main system and connected by capillary tube to a remote bulb. This remote bulb is fixed in close contact with the suction gas line at the outlet from the evaporator and is responsive to changes in refrigerant vapour temperature at this point. These valves are the most commonly employed (as in the automatic freon system Figure 11.3) and are suitable for the control of systems where changes in the loading are frequent.
Unlike the automatic valve, based on constant evaporator pressure, the thermostatic valve is based on a constant degree of superheat in the vapour at the evaporator outlet, so enabling the evaporator at any load to be kept correctly supplied with liquid refrigerant without any danger of liquid cany over to the suction line and thence to the compressor. The aperture in the expansion valve is controlled by pressure variation on the top of a bellows. This is effective through the push pins (Figure 11.12) and tends to open the valve against the spring. Spring pressure is set during manufacture of the valve and should not be adjusted.
The pressure on the bellows is from a closed system of heat sensitive fluid in a bulb and capillary connected to the top of the bellows casing. The bulb (Figure 11.13) is fastened to the outside of the evaporator outlet so that temperature changes in the gas leaving the evaporator are sensed by expansion or contraction of the fluid. Ideally the gas should leave with 6° or 7°C of superheat. This ensures that the refrigerant is being used efficiently and that no liquid reaches the compressor. A starved condition in the evaporator will result in a greater superheat which through expansion of the liquid in the bulb and capillary, will cause the valve to open further and increase the flow of refrigerant.
A flooded evaporator will result in lower superheat and the valve will decrease the flow of refrigerant by closing in as pressure on the top of the bellows reduces. Saturation temperature is related to pressure but the addition of superheat to a gas or vapour occurs after the latent heat transaction has ended. The actual pressure at the end of an evaporator coil is produced inside the bellows by the equalizing line and this is in effect more than balanced by the pressure in the bulb and capillary acting on the outside of the bellows. The greater pressure on the outside of the bellows is the result of saturation temperature plus superheat.
The additional pressure on the outside of the bellows resulting from superheat overcomes the spring loading which tends to close the valve. A hand regulator is fitted for emergency use. It would be adjusted to give a compressor discharge pressure such that the equivalent condensing temperature shown by the gauge at the compressor outlet was about 7°C above that of the
sea-water temperature and the suction gauge showed an equivalent evaporating temperature about the same amount below that of the evaporator.
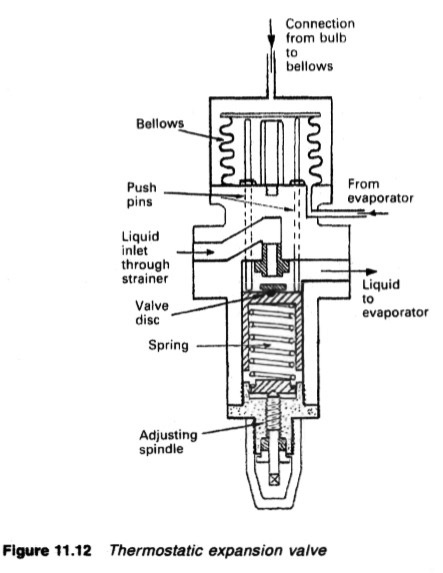
Figure 11.12 :Thermostatic expansion valve
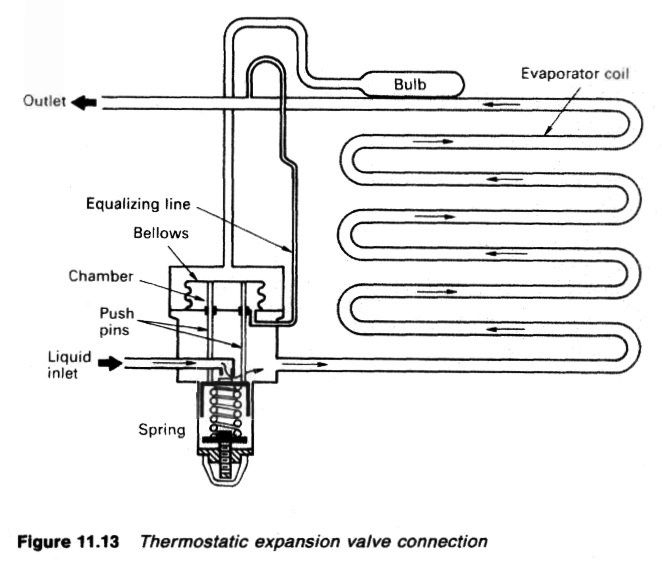
Figure 11.13 : Thermostatic expansion valve connection
Summarized below various refrigeration system components, working process and maintenance guideline:
- Automatic direct expansion refrigeration- vapour compression
The basic components of any refrigeration system (Figure 11.1) working on the
vapour compression cycle, are the compressor, condenser, expansion valve,
evaporator and the refrigerant fluid which is alternately vaporized and liquefied
during the refrigeration cycle. The temperature at which a fluid boils or
condenses, is known as the saturation temperature and varies with pressure....more
-
Choice of refrigerants
Theoretically, almost any liquid can be used as a refrigerant if its pressure/temperature relationship is suitable for the conditions. Although no perfect refrigerant is known, there are certain factors which determine a refrigerant's desirability for a particular duty and the one selected should possess as many as possible of the following
characteristics.....more
-
Refrigeration systems - Chamber cooling arrangements
To avoid having an extended refrigeration circuit for cargo cooling, a brine system can be used. The brine is cooled by the evaporator and in turn cools grids or batteries. Grids provide cooling which relies on convection and conduction but air circulated through brine batteries provides a positive through cooling effect.
.....more
-
Refrigeration system components
Marine condensers are generally of the shell and tube type, designed for high pressures. There may a few coil-in-casing or other types still in use. The coolant passes through the tubes with refrigerant condensing on the outside......more
-
Refrigeration system compressors
Refrigeration compressors are usually either reciprocating, or of the rotary
screw displacement type. Centrifugal and rotary vane compressors have also
been used.....more
-
Refrigeration systems expansion valves
The expansion valve is the regulator through which the refrigerant passes from the high pressure side of the system to the low pressure side. The pressure drop causes the evaporating temperature of the refrigerant to fall below that of the evaporator. .....more
- Monitoring instruments,CO2 measurement & Heat leakage and insulation test
All necessary cargo temperature readings are obtained on modern reefers and container ships on a data logger which makes an automatic record. The temperatures and pressures relating to refrigerant gas and liquid, cooling water, brine and the ambient are also required. Most of these are obtained from direct reading instruments.
.....more
- Marine condenser assembly
The temperature of the refrigerated spaces with a direct expansion system is controlled between limits through a thermostatic switch and a solenoid valve which is either fully open to permit flow of refrigerant to the room evaporator, or closed to shut off flow. The solenoid valve is opened when the sleeve moving upwards due to the magnetic coil hits the valve spindle tee piece and taps the valve open.....more
- Comparison between refrigerants R717 ammonia & R744 carbon dioxide
The ammonia used for refrigeration systems based on the use of a compressor,
condenser, expansion valve and an evaporator (Figure 11.2) is dry (anhydrous)
in that there is no water in solution with it. It has the chemical formula NH3 but
as a refrigerant, it is coded with the number R717....more
-
Container cooling system
The air is cooled either by brine or direct expansion batteries and the containers are arranged so that one cooler can maintain a stack of containers at a given temperature. The temperature of the return air duct for each container is monitored.....more
Home page||Cooling ||Machinery||Services ||Valves ||Pumps ||Auxiliary Power ||Propeller shaft ||Steering gears ||Ship stabilizers||Refrigeration||Air conditioning ||Deck machinery||Fire protection||Ship design
||Home ||
General Cargo Ship.com provide information on cargo ships various machinery systems -handling procedures, on board safety measures and some basic knowledge of cargo ships that might be useful for people working on board and those who working in the terminal. For any remarks please
Contact us
Copyright © 2010-2016 General Cargo Ship.com All rights reserved.
Terms and conditions of use
Read our privacy policy|| Home page||