Home page||Refrigeration system||
Refrigeration systems- Monitoring instruments,CO2 measurement & Heat leakage and insulation test
Instruments:
It is essential to measure and log the temperature of refrigerated cargo to ensure that the correct conditions are maintained and also to provide a record should there be complaints from a shipper. Mercury or spirit thermometers suspended from screwed plugs in vertical steel tubes with perforations hung in the cold chamber have been replaced by remote reading devices.
Electrical resistance and electronic self-balancing thermometers use the principle of the Wheatstone bridge. The former rely on a galvanometer to indicate a balance. In the latter the unbalanced current causes an electric motor to adjust the resistance.
All necessary cargo temperature readings are obtained on modern reefers and container ships on a data logger which makes an automatic record. The temperatures and pressures relating to refrigerant gas and liquid, cooling water, brine and the ambient are also required. Most of these are obtained from direct reading instruments.
Carbon dioxide measurement
Carbon dioxide concentration in the cargo chamber is important when fruit or chilled beef is carried. The electrical CO2 indicator (Figure 11.23) operates on the principle that CO2 is a better heat conductor than air.
A sample of air with CO2 content, is passed over platinum resistance wires carrying a constant heating current. Between the sample chambers CO2 is absorbed to give a differential reading. The wire temperature is less when CO2 content is higher. The temperature difference is detected on a Wheatstone bridge circuit through a suitably calibrated milliammeter which gives a direct CO2 reading.
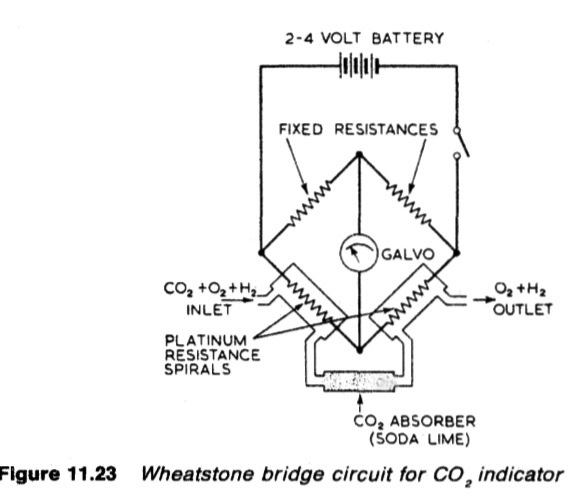
Figure : Wheatstone bridge circuit for CO2 indicator
Defrosting
This very necessary operation presents no difficulty when the cooling medium is brine. All that is required is a brine heater (Figure 11.24) with brine pump and circuits to circulate hot brine through the coolers. In direct expansion systems, defrosting can be effected by separate electric heaters installed in the evaporator grids (see Figure 11.3) or by providing a means of bypassing the condenser so that hot gas from the compressor circulates the evaporator directly.
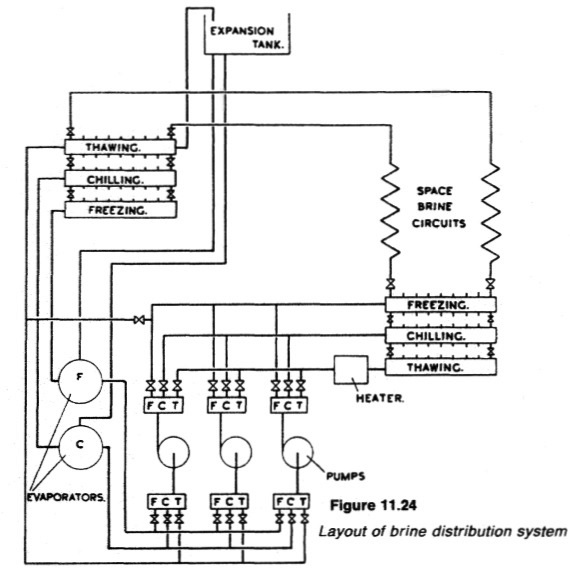
Figure : Layout of brine distribution system
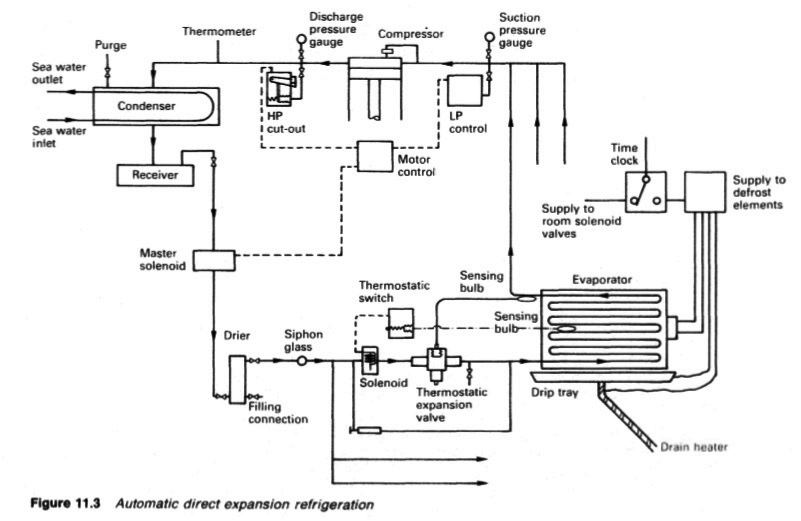
Figure : Automatic direct expansion refrigeration
Heat leakage and insulation
The total load on a cargo refrigerating plant is the sum of:
1 surface heat leakage from the sea and surrounding air; 2 deck and bulkhead edge leakage from the same sources; 3 heat leakage from surroundings into system pipes; 4 heat equivalent of fan and some brine pump power; 5 cooling of cargo not precooled at loading; 6 respiratory heat of live cargoes; 7 heat introduced by air refreshment of live cargoes.
The load arising from 1, 2 and 3 can be much reduced by the efficient use of insulation. A number of materials are used for this including slab cork, glass and
mineral wools, expanded plastics, aluminium foil and polyurethane. The latter, although generally most costly, is the best insulator, having the lowest coefficient of conductivity, with the further advantages of being impervious to air leaks and almost impervious to the passage of vapour, when the material is foamed in situ, Materials which contain CFCs should not be specified.
Some rigid urethane foams (polyisocyanates and polyurethanes) and expanded polystyrene or phenolics may contain CFCs. These materials are used for their low thermal conductivity, high resistance to the passage of vapour, good mechanical properties and ease of construction. They can be produced so as to be free of CFCs but with higher thermal conductivity. All of the materials mentioned have to be enclosed by linings for protection and the prevention of air leakage. The design and construction of the linings makes a greater contribution to the efficiency of an installation.
Insulation test
The heat balance test which replaced an earlier unsatisfactory version, was introduced by the major Classification Societies in 1947. In this trial, temperatures in the refrigerated spaces are reduced to a specified figure and then after a lapse of time sufficient to remove all residual heat from the insulation and structure, the spaces are maintained at constant temperature for at least six hours by varying the compressor output.
During this period all temperatures and pressures, speeds and electrical consumption of compressors, fans and pumps are carefully logged and the compressors' output is noted from appropriate tables. From this information it is possible to compare the efficiency of the insulation with the theoretical estimate made during the design stage and also to decide whether or not the installation can maintain these temperatures in maximum tropical sea and ambient conditions. Obtaining the theoretical estimate entails taking each external surface of the individual chambers separately and considering all factors affecting the heat leakage.
These factors include the pitch, depth and width of face of all beams, frames and stiffeners buried in the insulation, the type of grounds securing the linings, the presence of which have their effect in reducing the effective depth of the insulation.
Hatches, access doors, bilge limbers, air and sounding pipes also have their effect on heat leakage and must come into consideration. It should be noted that in these calculations the laboratory value of the insulation is generally increased by about 25% to allow for deficiencies in fitting.
It has been found that the overall co-efficient of heat leakage in well insulated installations can vary between 0.454 W/m2/°C for 'tweendecks in small lightly framed ships and 0.920 W/m2/°C for fully refrigerated moderate sized ships having deep frames with reverse angles. Where there are also buried air ducts, the effective depth of the insulation may reduce to little more than zero.
Summarized below various refrigeration system components, working process and maintenance guideline:
- Automatic direct expansion refrigeration- vapour compression
The basic components of any refrigeration system (Figure 11.1) working on the
vapour compression cycle, are the compressor, condenser, expansion valve,
evaporator and the refrigerant fluid which is alternately vaporized and liquefied
during the refrigeration cycle. The temperature at which a fluid boils or
condenses, is known as the saturation temperature and varies with pressure....more
-
Choice of refrigerants
Theoretically, almost any liquid can be used as a refrigerant if its pressure/temperature relationship is suitable for the conditions. Although no perfect refrigerant is known, there are certain factors which determine a refrigerant's desirability for a particular duty and the one selected should possess as many as possible of the following
characteristics.....more
-
Refrigeration systems - Chamber cooling arrangements
To avoid having an extended refrigeration circuit for cargo cooling, a brine system can be used. The brine is cooled by the evaporator and in turn cools grids or batteries. Grids provide cooling which relies on convection and conduction but air circulated through brine batteries provides a positive through cooling effect.
.....more
-
Refrigeration system components
Marine condensers are generally of the shell and tube type, designed for high pressures. There may a few coil-in-casing or other types still in use. The coolant passes through the tubes with refrigerant condensing on the outside......more
-
Refrigeration system compressors
Refrigeration compressors are usually either reciprocating, or of the rotary
screw displacement type. Centrifugal and rotary vane compressors have also
been used.....more
-
Refrigeration systems expansion valves
The expansion valve is the regulator through which the refrigerant passes from the high pressure side of the system to the low pressure side. The pressure drop causes the evaporating temperature of the refrigerant to fall below that of the evaporator. .....more
- Monitoring instruments,CO2 measurement & Heat leakage and insulation test
All necessary cargo temperature readings are obtained on modern reefers and container ships on a data logger which makes an automatic record. The temperatures and pressures relating to refrigerant gas and liquid, cooling water, brine and the ambient are also required. Most of these are obtained from direct reading instruments.
.....more
- Marine condenser assembly
The temperature of the refrigerated spaces with a direct expansion system is controlled between limits through a thermostatic switch and a solenoid valve which is either fully open to permit flow of refrigerant to the room evaporator, or closed to shut off flow. The solenoid valve is opened when the sleeve moving upwards due to the magnetic coil hits the valve spindle tee piece and taps the valve open.....more
- Comparison between refrigerants R717 ammonia & R744 carbon dioxide
The ammonia used for refrigeration systems based on the use of a compressor,
condenser, expansion valve and an evaporator (Figure 11.2) is dry (anhydrous)
in that there is no water in solution with it. It has the chemical formula NH3 but
as a refrigerant, it is coded with the number R717....more
-
Container cooling system
The air is cooled either by brine or direct expansion batteries and the containers are arranged so that one cooler can maintain a stack of containers at a given temperature. The temperature of the return air duct for each container is monitored.....more
Home page||Cooling ||Machinery||Services ||Valves ||Pumps ||Auxiliary Power ||Propeller shaft ||Steering gears ||Ship stabilizers||Refrigeration||Air conditioning ||Deck machinery||Fire protection||Ship design
||Home ||
General Cargo Ship.com provide information on cargo ships various machinery systems -handling procedures, on board safety measures and some basic knowledge of cargo ships that might be useful for people working on board and those who working in the terminal. For any remarks please
Contact us
Copyright © 2010-2016 General Cargo Ship.com All rights reserved.
Terms and conditions of use
Read our privacy policy|| Home page||