Home page||Marine Pumps ||
Axial flow pumps - Procedure for marine pumps
An axial flow pump is one in which a screw propeller is used to create an increase in pressure by causing an axial acceleration of liquid within its blades. The incidental rotation imparted to the liquid is converted into straight axial movement by suitably shaped outlet guide vanes. Axial flow pumps are sometimes classed with centrifugal pumps although centrifugal force plays no useful part in the pumping action.(Figure 1)
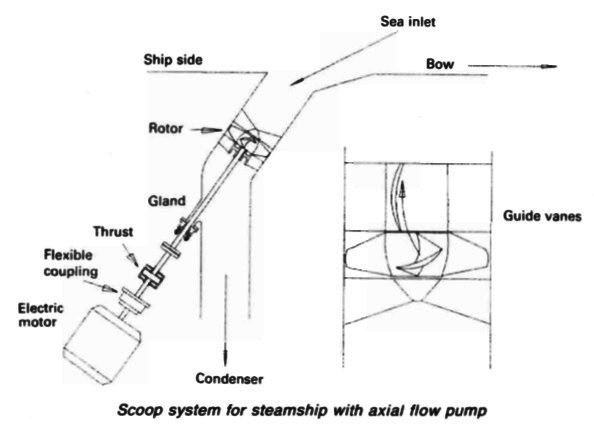
Figure 1:Scoop system for steamship with axial flow pump
A comparison of discharge characteristics (Figures 2 and 3) shows that H/Q and working efficiency characteristics for the two pumps are quite different. The discharge characteristics (Figure 2) drawn in each case for constant speed show those for the axial flow pump with a solid line and those for the centrifugal with a broken line.
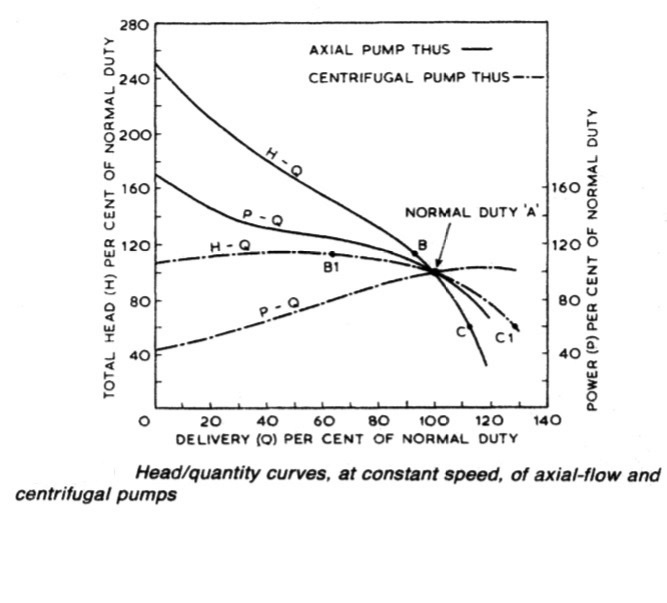
Figure 2: Head/quantity curves, at constant speed, of axial-flow and centrifugal pumps
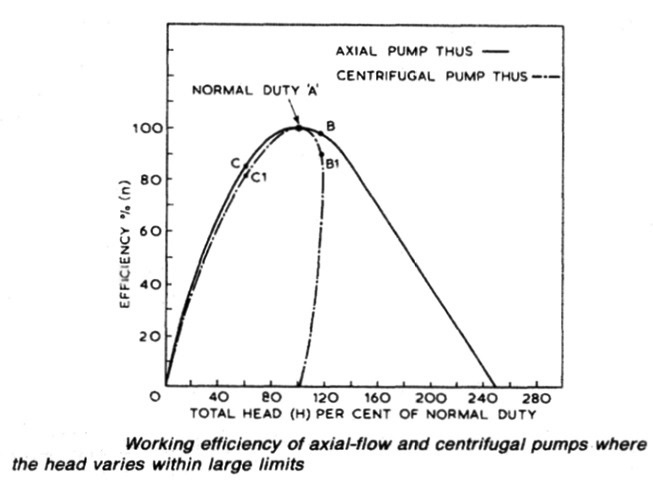
Figure 3: Working efficiency of axial-flow and centrifugal pumps where the head varies within large limits
Axial flow pump working method
Starting from the point of normal duty, throttling of the discharge of an axial flow pump reduces the flow but also causes a rise in pressure and power. With the valve closed and zero discharge, the head can be about three times greater and absorbed power about doubled. The action of throttling to reduce throughput would overload the electric
motor and cause operation of protective devices.
The throughput needs to be controlled in another way or the pump motor must be over-rated. In fact, the closing in of the discharge tends to cause water hammer. If the discharge of the centrifugal pump is closed in, as previously described, the pressure rises by a moderate amount and power demand actually drops.
Beyond the point of normal duty, the axial pump power requirement decreases with lower head and delivery increases by a modest amount. For the centrifugal pump operating at lower head, the greater throughput is matched by a rise in absorbed power (although there is a marginal fall off beyond normal duty).
The centrifugal pump electric motor can be overloaded at low head and high throughput — the opposite condition for overload of an axial pump. The axial pump (Figure 3) retains reasonable efficiency over a wider head range, than the centrifugal pump.
There are three other features of the axial flow pump not indicated by the graph but of particular importance in their application. These are:
1 Under the low head (2.5 to 6.2 m) high throughput (2800-9500 mVhr) conditions commonly required by main condensers, an axial flow pump with a higher speed than an equally matched centrifugal purnp can be used. The electric motor for the pump, can be of smaller size.
2 The pump will idle and offer little resistance when a flow is induced through it by extremal means.
3 The pump is reversible. This combination of characteristics makes the axial flow pump ideal for condenser circulating duties, especially in conjunction with a scoop injection (Figure 1) where the motion of the ship under normal steaming conditions is
sufficient to induce a flow through the idling pump and the condenser. Reversibility and high throughput make it ideal for heeling and trimming duties.
An axial flow pump may be fitted on the straight transfer pipe between tanks installed for this purpose. When used for sea-water circulation the pump will normally have a gunmetal casing; for heeling and trimming applications it is more usual to find pumps with cast iron casings. Impellers are of aluminium-bronze, guide vanes of gunmetal and the shaft of stainless steel, with a renewable stainless steel sleeve in way of the bush.
Axial pump cavitation and supercavitating pumps
The hydrofoil section of conventional axial pump blades (upper right Figure 4), like those of propellers, promotes a severe drop in pressure at the leading edge and on the surface of the suction side, while producing positive pressure on the discharge surface. The blade shape enhances operation but cavitation can be a problem mainly on the suction surface of pumps rotating at very high speed.
Cavitation occurs when a drop in pressure at the leading edge and across the blade surface is sufficient to produce vapour (and air if present) from the liquid. The pressure of the liquid increases as it passes through the pump and vapour pockets or bubbles, subjected to positive pressure, then collapse, as vapour is re-absorbed back into the liquid.
Erosion is caused because vapour pocket collapse is very rapid and liquid rushes in with considerable force. The impact damages the metal surface. An axial flow pump with hydrofoil shaped blades, which operates at excessive speed, also creates a demand for rapid inflow of the liquid being pumped. Flow may not match the demand with resulting loss of efficiency which may be compounded by cavitation and erosion on blade surfaces.
Supercavitating pumps have blades of a wedge cross section (lower right Figure 4) to produce a different cavitation pattern. A drop in pressure is not pronounced at the leading edge; it is minimal over the full area of the suction side of the blades and exaggerated only at the trailing edge. Vapour pockets persist until clear of the blade and collapse where they cause no damage.
The supercavitating type of axial flow pump operates at high speed but generates low discharge head. As a small, light-weight, high-speed pump, it is used for fuel transfer in aircraft and rockets. It is also used as a suction booster or inducer for conventional centrifugal cargo pumps in liquefied gas carriers because it can handle liquids at, or near their vapour pressure, with higher speeds than can conventional pumps.
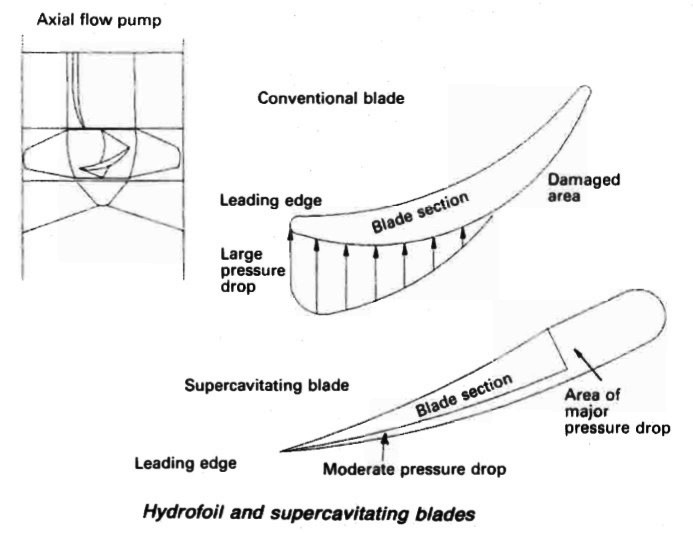
Figure 4: Hydrofoil & supercavitating blades
Summarized below some of the basic procedure of marine pumps and pumping system onboard :
- Axial flow pumps
An axial flow pump is one in which a screw propeller is used to create an increase in pressure by causing an axial acceleration of liquid within its blades. The incidental rotation imparted to the liquid is converted into straight axial movement by suitably shaped outlet guide vanes.....
- centrifugal pumps
Rotation of a centrifugal pump impeller causes the liquid it contains to move outwards from the centre to beyond the circumference of the impeller. The revolving liquid is impelled by centrifugal effect.....
- Centrifugal pump cavitation
Because of their self-priming ability, positive displacement pumps are widely used for lubricating oil duties. This practice is completely satisfactory in installations where the pump speed is variable but when the pump is driven by a constant speed a.c. motor it is necessary to arrange a bypass which can be closed in to boost flow. ....
- Gear pumps
Diesel engine and gearbox lubrication systems are normally supplied by gear
pumps which are independently driven for large slow speed engines and
stand-by duties but usually shaft driven for medium and high speed engines.
Gear pumps are also used for fuel and oil transfer, boiler combustion systems
and other duties.....
- General pumping system characteristics
A pump divides its pipe system into two distinct parts, each with different
characteristics. These are the suction and discharge sides. On the suction side
the drop in pressure that can be produced by a pump is limited to that of an
almost perfect vacuum. On the discharge side there is theoretically, no limit to
the height through which a liquid can be raised.....
- General purpose pumps
Single entry general purpose pumps are used for salt and fresh water circulating and also for bilge and ballast duties. The impeller is suspended from the shaft with no bottom support. ....
- Lobe pumps
Lobe pumps as manufactured by Stothert and Pitt have inner and outer
elements which rotate in a renewable liner fitted in the pump body. The inner
rotor is eccentric to the outer and is fitted to a shaft located by bearings in the
pump covers....
- Marine pumps construction
Marine pumps are usually installed with the shaft vertical and the motor above the pump. This positions the pump as low as possible for the best NPSH, takes up the least horizontal space and leaves the electric motor safer from gland or other leakage.....
- Pumps erosion
A pump handling liquids which contain abrasives, will suffer erosion on all internal surfaces, including bearings and shaft seals. The sea-water circulating pumps of ships operating in waters that contain large quantities of silt and sand
require frequent renewal of shaft seals or packing, also of shaft sleeves in way of the gland and bearings.....
- Rotary displacement pump
Positive displacement rotary pumps rely on fine clearances between moving
parts for their efficient operation. Excessive wear or erosion of parts, due to
friction contact or the presence of abrasives, is avoided by employing this type
of pump for specialized rather than general duties......
- Screw pumps
Both double-screw pumps, in which the screws are driven in phase by timing
gears , and triple screw pumps , in which the centre
screw is driven and the outer screws idle are used at sea especially for pumping
high viscosity liquids such as oil and some liquid cargoes.....
Home page||Cooling ||Machinery||Services ||Valves ||Pumps ||Auxiliary Power ||Propeller shaft ||Steering gears ||Ship stabilizers||Refrigeration||Air conditioning ||Deck machinery||Fire protection||Ship design
||Home ||
General Cargo Ship.com provide information on cargo ships various machinery systems -handling procedures, on board safety measures and some basic knowledge of cargo ships that might be useful for people working on board and those who working in the terminal. For any remarks please
Contact us
Copyright © 2010-2016 General Cargo Ship.com All rights reserved.
Terms and conditions of use
Read our privacy policy|| Home page||