Home page||Marine Pumps ||
Screw pumps for cargo ships- single,double & triple screw pumps
Both double-screw pumps, in which the screws are driven in phase by timing
gears (Figure 1: two screw displacement pump), and triple screw pumps (Figure 2), in which the centre
screw is driven and the outer screws idle are used at sea especially for pumping
high viscosity liquids such as oil and some liquid cargoes.
Being self-primning
and able to pump liquid and vapour without loss of suction they are
particularly useful when draining tanks of high vapour pressure liquids. They
are suitable for operation at high rotational speed (units are in operation with
speeds of 3500 rev/min, delivering over 1000 litres/min) and can thus be easily
matched with standard electric motors.
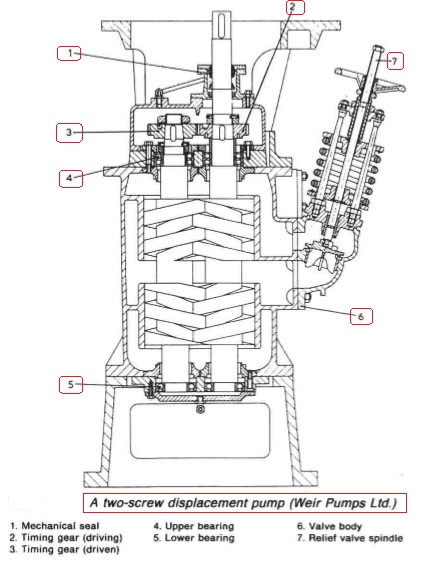
Figure 1: Two screw displacement pump
In the IMO triple screw pump the centre screw is driven mechanically,
through a flexible coupling. The two outer screws are driven by the fluid
pressure and act purely as seals. The screws work in a renewable cast iron
sleeve mounted in a cast iron pump casing. When the screws rotate, their close
relation to each other creates pockets in the helices; these pockets move axially
and have the same effect as a piston moving constantly in one direction. These
pumps work well at high pressure and with high viscosity fluids (up to 4000
centistokes). The axial thrust on the power rotor is balanced hydraulically, that
of the idlers by thrust washers.
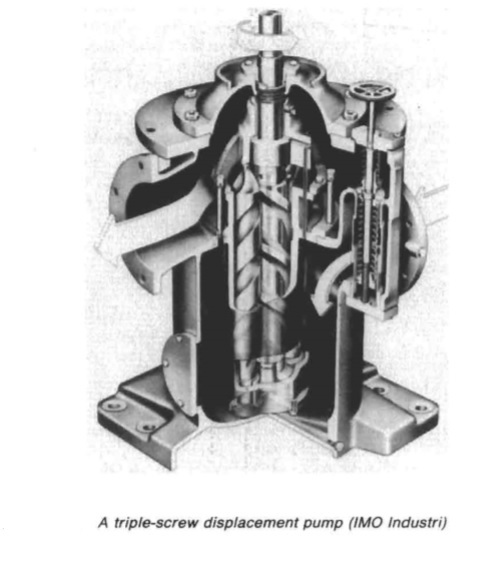
Figure 2: A triple-screw displacement pump (IMO Indus)
Double-screw pump with timing gears
This type of pump can be mounted either horizontally or vertically. Pumping is
effected by two intermeshing screws rotating within a pump casing. Each
screw shaft has a right and a left hand screw which ensures axial hydraulic
balance, there being no load imposed on the location bearing.
Metal contact is avoided by driving the screwshaft through hardened and
ground timing gears. Once the casing has been filled with liquid, the pump is
self-priming and ready for operation. Displacement on pumping occurs when
the screws are rotated and liquid is drawn into the screws at the outer ends and
pumped inwards to the discharge located at rotor mid-length. The discharge is
without pulsation.
When pumps are installed for handling non-corrosive liquids of reasonable
lubricity, it is normal to find units with internal bearings. For handling corrosive
chemicals, liquids with a lack of lubricity and/or high very high viscosity,
designs incorporating outside bearings (Figure 3) which can be independently
lubricated would be used.
Pumps with inside bearings are shorter and lighter than their outside bearing
counterparts and have only one shaft seal as against four.
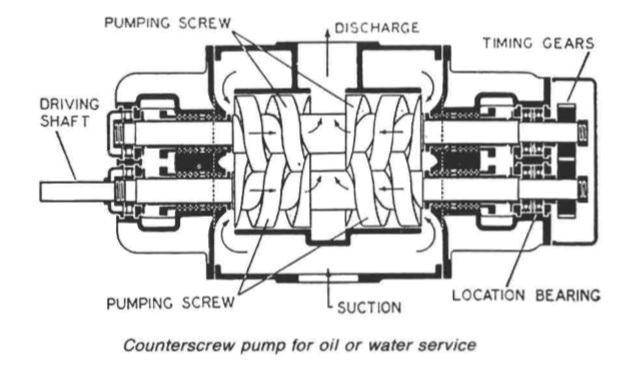
Figure 3: counterscrew-pump
Shaft sealing
The double-screw pump (Figure 1) shaft sealing is effected by either
mechanical seals or packed glands. The shaft seal is at the suction end of the
pump, so that seals are subjected only to low pressure or vacuum.
Shaft seals must ensure leak-free operation of cargo pumps for toxic and
corrosive liquids. Provision is usually made for mechanical seals to be cooled
and lubricated by the pumped liquid. For installations in pumproorns an
external header may be fitted to service the seal.
Materials
For the general range of liquids handled, cast iron is suitable for the casing and
bearing housings. Screwshafts are normally of high grade carbon steel or
stainless steel. Materials having high corrosion resistant qualities such as
stainless steel EN 58 J and Hastelloy are used. If screws are not in direct contact
they will not be scuffed.
Protection
Since screw pumps are essentially displacement pumps and will produce
increasing pressure until rupture or drive failure occurs it is necessary to
safeguard the pump, prime mover and its associated pipework against the
event of a discharge line valve closure. The pumps are equipped with full flow
relief valves capable of bypassing the entire throughput of the pump. This is for
safety purposes only however, and should only operate for a short time
otherwise excessive liquid/pump temperatures will result.
The valve may be
fitted with either manual or automatic control to facilitate starting up under a
no load condition. This is necessary where the discharge system is under
pressure, to avoid excessive starting torque (electrical load) and long run-up
times.
Relief valves are also often fitted with automatic volume control valves,
which control the output of the pump in order to maintain either a constant
pressure or a vacuum at a specific point in the system — as in diesel engine
lubricating oil supply — to ensure constant pressure at engine inlet irrespective
of oil viscosity.
When hot or viscous liquids are handled it may be necessary to preheat the
casing of a pump already filled with liquid. Means for heating are available, for
example electric immersion heaters or a coil through which low pressure steam
or hot oil is circulated.
Single screw pumps
Oil and water separators require delivery from low capacity, smooth flow bilge
pumps. The mono purnp, with its corrosion resisting rotor and a stator of
natural or synthetic rubber, is frequently used.
Summarized below some of the basic procedure of marine pumps and pumping system onboard :
- Axial flow pumps
An axial flow pump is one in which a screw propeller is used to create an increase in pressure by causing an axial acceleration of liquid within its blades. The incidental rotation imparted to the liquid is converted into straight axial movement by suitably shaped outlet guide vanes.....
- centrifugal pumps
Rotation of a centrifugal pump impeller causes the liquid it contains to move outwards from the centre to beyond the circumference of the impeller. The revolving liquid is impelled by centrifugal effect.....
- Centrifugal pump cavitation
Because of their self-priming ability, positive displacement pumps are widely used for lubricating oil duties. This practice is completely satisfactory in installations where the pump speed is variable but when the pump is driven by a constant speed a.c. motor it is necessary to arrange a bypass which can be closed in to boost flow. ....
- Gear pumps
Diesel engine and gearbox lubrication systems are normally supplied by gear
pumps which are independently driven for large slow speed engines and
stand-by duties but usually shaft driven for medium and high speed engines.
Gear pumps are also used for fuel and oil transfer, boiler combustion systems
and other duties.....
- General pumping system characteristics
A pump divides its pipe system into two distinct parts, each with different
characteristics. These are the suction and discharge sides. On the suction side
the drop in pressure that can be produced by a pump is limited to that of an
almost perfect vacuum. On the discharge side there is theoretically, no limit to
the height through which a liquid can be raised.....
- General purpose pumps
Single entry general purpose pumps are used for salt and fresh water circulating and also for bilge and ballast duties. The impeller is suspended from the shaft with no bottom support. ....
- Lobe pumps
Lobe pumps as manufactured by Stothert and Pitt have inner and outer
elements which rotate in a renewable liner fitted in the pump body. The inner
rotor is eccentric to the outer and is fitted to a shaft located by bearings in the
pump covers....
- Marine pumps construction
Marine pumps are usually installed with the shaft vertical and the motor above the pump. This positions the pump as low as possible for the best NPSH, takes up the least horizontal space and leaves the electric motor safer from gland or other leakage.....
- Pumps erosion
A pump handling liquids which contain abrasives, will suffer erosion on all internal surfaces, including bearings and shaft seals. The sea-water circulating pumps of ships operating in waters that contain large quantities of silt and sand
require frequent renewal of shaft seals or packing, also of shaft sleeves in way of the gland and bearings.....
- Rotary displacement pump
Positive displacement rotary pumps rely on fine clearances between moving
parts for their efficient operation. Excessive wear or erosion of parts, due to
friction contact or the presence of abrasives, is avoided by employing this type
of pump for specialized rather than general duties......
- Screw pumps
Both double-screw pumps, in which the screws are driven in phase by timing
gears , and triple screw pumps , in which the centre
screw is driven and the outer screws idle are used at sea especially for pumping
high viscosity liquids such as oil and some liquid cargoes.....
Home page||Cooling ||Machinery||Services ||Valves ||Pumps ||Auxiliary Power ||Propeller shaft ||Steering gears ||Ship stabilizers||Refrigeration||Air conditioning ||Deck machinery||Fire protection||Ship design
||Home ||
General Cargo Ship.com provide information on cargo ships various machinery systems -handling procedures, on board safety measures and some basic knowledge of cargo ships that might be useful for people working on board and those who working in the terminal. For any remarks please
Contact us
Copyright © 2010-2016 General Cargo Ship.com All rights reserved.
Terms and conditions of use
Read our privacy policy|| Home page||